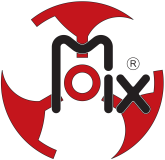
MIX SRL UNIPERSONALE - MIXER MACHINES
MIX was established in 1990 with a very specific entrepreneurial approach: to design and produce mixing systems suitable to mix and process various types of products, focusing on the utmost quality and reliability.
Its headquarters are located in Cavezzo, in the province of Modena, in the heart of Italy’s most important district for the mechanical industry.
Thanks to a Staff consisting of highly qualified technicians, in just a few years MIX has managed to expand its product range (Filtering, Interception, Monitoring, Transport and Extraction) and to establish itself on an international market that is both challenging and competitive, combining constant Research with ongoing Innovation and a targeted Development Programme. Along with these efforts, the choice not to provide Systems but rather Components and Processing Machines for plant design, has considerably improved its results.
RANGE OF “MIX” PRODUCTS FOR FOOD CONTACT APPLICATIONS
Always attentive to the needs of its Customers, MIX developed a new range of industrial mixers for food contact applications. All parts in contact with food products have its own declaration of conformity, for use in food application. The design of the mixers aims to avoid the deposit of food products in hidden areas and to facilitate the complete cleaning of each part of the mixer. In its mission, MIX stands not merely as a supplier, but as a reliable partner; for this reason MIX focuses its research and development activities on the needs of its Customers. Recently, MIX enhanced its internal Testing Facility with brand new machineries and is now able to execute trials with harder parameters in terms of Temperature, Pressure and Vacuum. Powders, Granules, Fibers, Pastes can be tested in the new laboratory, even in classified hazardous atmosphere (ATEX). The handling of chemical reactions, the measurement of moisture content of the products and the increase or decrease of pressure and temperature in the mixer is now fully automated. MIX Laboratory allows the control of all parameters, during every step of the process. Thanks to the new laboratory, it is now much easier to determine the characteristics of each raw material and, therefore, identify the most suitable mixing techniques for obtaining the desired final result. At MIX every mixer is tailored and custom manufactured, in order to satisfy even the most demanding and specific requirements. Following this task, MIX developed a new range of industrial ploughshare mixers equipped with fully extractable rotor shaft. This innovative solution enables the operator to easily access any point inside the mixing chamber and allows to obtain the complete cleaning of the mixing wall and the rotor shaft, drastically cutting the “non-productive time”. Main possible customizations are: double jacket with heat exchanger; side mounted intensifiers; liquid injection system. These features make the new mixers appropriate for many uses in several fields of application, where cleaning of the equipment at each change of recipe holds a great importance. This series of mixer with fully extractable rotor shaft is positioned at top range, intended for customers who consider the quality of their product an essential characteristic to distinguish themselves in the market.
Beside mixers, MIX developed new series of Dust Collector, Loading Bellows, Butterfly Valves suitable for applications in food industry, with powder products. The main features are metal parts in contact with product in stainless steel AISI 304; non-metal parts in contact with product with declaration of conformity for food application. Dust Collectors have a specific design following the Good Manufacturing Practice; the filtering elements can be removed easily from the side door or from the top, thanks to the new fixing system without screws. The efficient jet pulse cleaning of filtering elements is controlled by the new MIX control panel, which can include a pressure differential gauge.
Certification Systems according to ISO 9001 – ISO 14001 – ISO 45001.