According to market research, ready to eat food in portable packaging with tasty and fresh product characteristics are meeting the expectation of today’s consumer’s demand. In current fast paced lifestyle, less time is available to prepare healthy snack at home for office or school mid-day break.
The other important aspect, packaging wise, is that consumer demand environment friendly packages, easy to dispose in different waste collection program. Considering these starting points we can certainly confirm that Cama, Clevertech and Tosa has jointly developed, produced and successfully commissioned near Rome, for an important multinational company in Food Consumer Sector, the production line which is producing and handling this innovative packages.
Let’s bring you through the production process to explain the combined innovation which leads to tremendous cost reduction with the environment friendly approach.
The flexible pouches, with integrated nozzle, are made of monolayer material, which is a fantastic innovation since it provides the consumer the possibility to easily and correctly dispose it in one waste bin without requiring to separate material for two different bins, because in the past, the packages were made of different materials assembled in a multilayer form.
As we are producing and handling monolayer material it gives saving in the material cost itself, as for its production process, less production passages are required.
Moving on to the processing and filling part, which has the biggest saving, the products are filled and sealed in aseptic condition.
This is another great innovation as it cut all the associated costs that usually are linked to the product pasteurization that is performed in autoclaves requiring automation, also with treatment time utilizing important energy quantity and with reduced space requirement in the production hall.
Summarizing, while excluding the pasteurization step, the capex costs are reduced to at least 40% as the tray loading/unloading and autoclave are not required, at the same time, looking at the total cost of ownership the estimated reduction is about 50%.
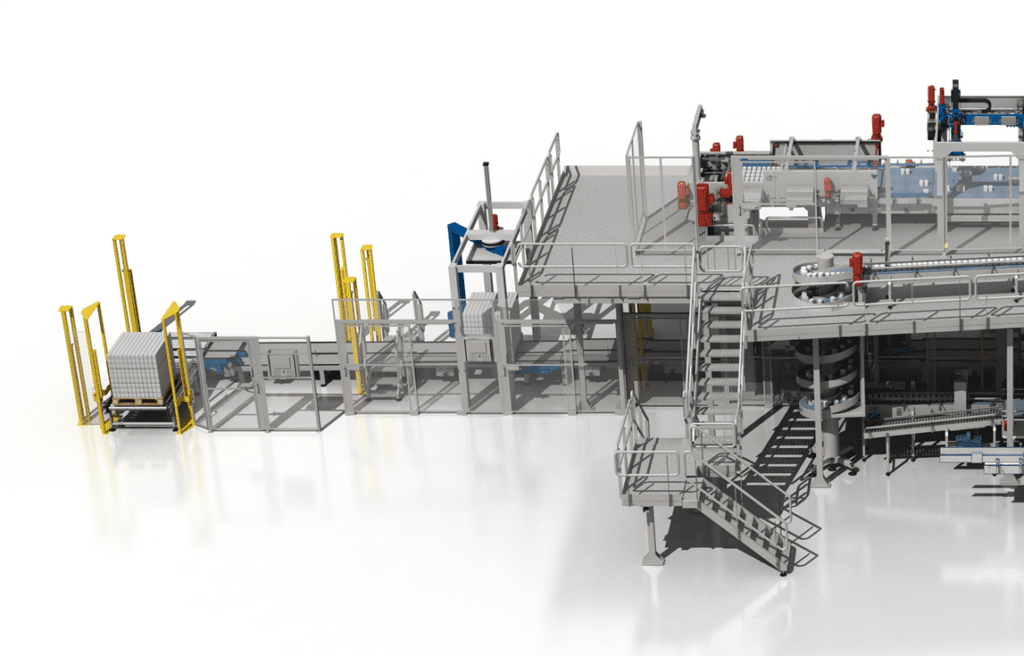
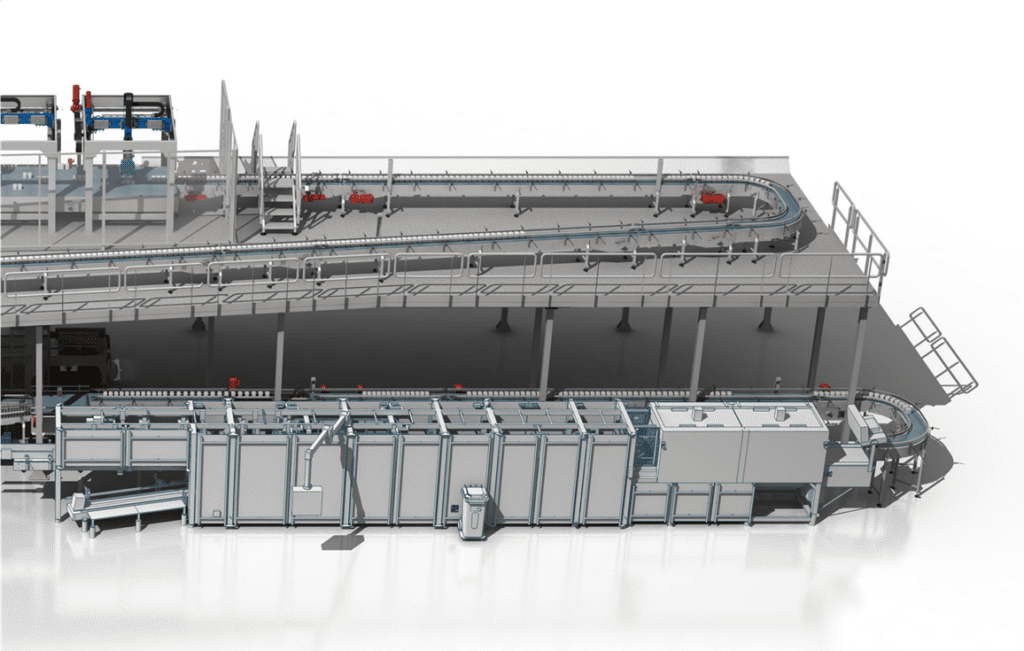
Once the primary package is filled and seal, Cama is placing the pouches in the packaging flow and their journey to the shelves begins. Cama’s system begins at the filler’s exit with the orderer, who determines the correct flow of the products and their orientation during the transport path.
The first operation is to transfer the Pouch to the SRP case: the products doypacks with caps (stand-up pouches ranging in weight from 85 to 180 g) are weighed, labeled, checked with an X-ray system for the presence of contaminants, and then sorted with the divider, which orders the products to the packaging lines for the creation of both types of format.
The Shelf Ready Packaging boxes (four pouches) are grouped and placed in corrugated cardboard wraparound boxes made from flat blanks (closed with hot glue).
SRP tertiary packaging is the second operation handled by Cama FW wrap around model very versatile, allowing to perform multiple tasks with a single machine. Cama FW model can create crates with dimensions up to a quarter of a pallet (400 X 300 mm) for products that require reduced packaging due to the demands of the large-scale retail trade.
Now the secondary package is carried into Clevertech system where there is the second weight check for the secondary packaging to assure that it is completely filled with all settled pouches. The cases are labelled with a print and apply system to have the full traceability along the production line.
The reject, positioned prior to the downstream of the line, is rejecting the packages with incorrect weight or non-readable labels. Further, the secondary packages are taken into a spiral elevator and transported them directly to the warehouse.
This design, yielded another big cost cutting in the total cost of ownership of the production line as originally the customer preferred to have the palletization near the primary packaging, but during the evaluation in project design development phase, with a win – win philosophy, it was decided to have an higher capex investment in conveyor which eliminates the use of forklift to move loaded pallet from production to warehouse.
At the end of line, performed in the high level palletizer Clevertech AC 520, the product is entering in a positive layer pattern forming with Lineflex manipulator which gives the possibilities to handle very small packages from 4 pouches per case up to collecting carton with 48-64 pouches.
The other flexibility from Clevertech, beside the product range handling, is in the production speed that can be doubled once another Lineflex in layer pattern forming is added to the existing one, in other words, adding a reduced Capex the line can be taken to double its performance.
The Clevertech system is complete tie sheet and slip sheet application and it integrate print and apply label to pallet in a seamless condition, which is connected to the print and apply to carton for a perfect integration and tracking to customer ERP and WMS.
The pallet stretch wrapper Tosa 090 integrated in the Clevertech supply, is installed with a system for vertical corner application, complete with 2 fixed corner posts storage units and n.1 automatic applicator useful for increasing the overall capacity or for using up to 2 different formats of corner posts, automatically selected according to the type of pallet to be stretch wrapped.
The machine guarantees outstanding performances and maximum stability for entry level productions: it is designed for low maintenance, ground level motor positioning for easy inspection and maintenance, for maximum flexibility and versatility of components to suit any layout configuration.
The philosophy currently applied on this machine provides that the design of each device will guarantee minimum maintenance, optimize costs, time saving, increase sustainability, safety and cleanliness.
DOWNLOAD HERE A FREE COPY OF FOOD PROCESSING 2-2022