Gravimetric methods have an advantage in content determination
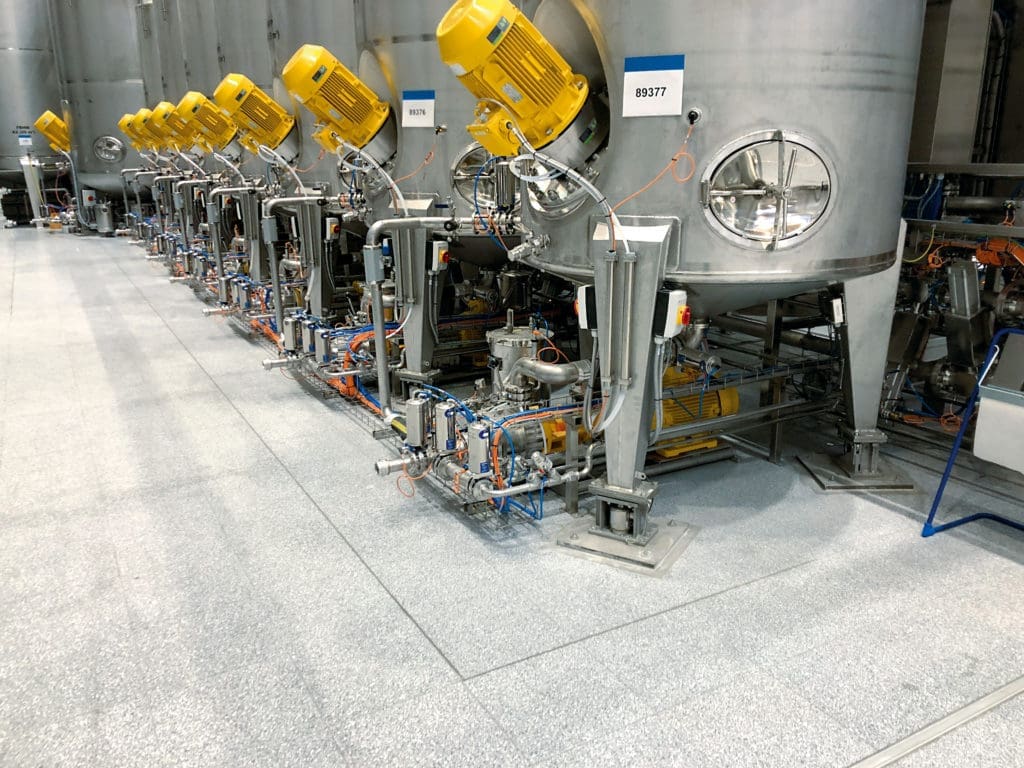
Due to their physical properties, bulk solids place high demands on the exact determination of the contents of a container and on quantity balancing in a processing operation. This applies equally to static weighing, for example in a tank, and to the dosing of free-flowing products.
Gravimetric, i.e. weight-determining, methods are an established method for determining the content of bulk materials. These weighing techniques offer the advantages that they work extremely precisely, have no direct contact with the product and record the weight of the bulk material independently of grain size, density and bulk density.
It is precisely this last advantage that becomes apparent when dosing bulk material. Here, volumetric dosing is available as an alternative, which measures the discharge by means of volume per time unit. However, the density of the dosing medium plays a decisive role in volumetric dosing. If the density of the material fluctuates during the discharge time, this inevitably leads to inaccuracies in the weight.

In a weight-controlled dosing system, integrated load cells measure the material to be dosed. The weight is therefore the decisive only measured variable. By means of a target/actual comparison that controls the dosing, gravimetric systems can automatically compensate for deviations in bulk density. This means that, in contrast to volumetric dosing, the conveying speed, for example the speed of the screw, can also be individually adjusted. With continuous discharge, gravimetric measuring methods are thus significantly more accurate, as the mass flow is measured per unit of time.
Additional accuracy is provided by dosing a batch into an intermediate hopper capable of measuring the discharged weight. Depending on the size, the intermediate hopper can be mounted directly on a static scale platform or on a structure with three load cells for ideal stability. Intelligent dosing algorithms control the discharge and allow target weights to be achieved extremely precisely and in the shortest possible time. The use of load cells based on strain gauge (DMS) technology is proven, reliable and low-maintenance. In a few simple steps, if requirements are observed in the mechanical design, then system accuracies of 0.1% are usually achievable. The pre-requisite for this is that the measuring level is horizontal to the ground and that supporting steel structures on the intermediate container are rigid.

Minebea Intec offers a wide portfolio of load cells for container and silo weighing in a wide range of applications. Standard applications can be carried out with proven bending rods and compact load cells including the corresponding installation kits. Containers or batching machines with low weights can be equipped with single point load cells. For special environmental conditions, special solutions are available for applications with vibrations, increased temperature operating range and for use in earthquake-prone areas. The Contego® weighing module, for example, is particularly suitable for applications with high demands on hygienic design, for example in the food sector or in pharmaceutical plant construction. In addition to their special design with integrated installation kit, these weighing modules also absorb lateral forces, this is a unique selling point in the market, so that the otherwise usual installation kit is completely unnecessary.
Minebea Intec has various weighing electronics for evaluating the measurement signal. These range from integration in a control cabinet on DIN rails with the PR5220 weighing transmitter and corresponding software application, to the Maxxis 4 process controller with integrated display for integration in a housing/cabinet and the Maxxis 5 as a desktop weighing controller. All these weighing electronics optionally offer a corresponding dosing application from simple single-component dosing to complex multi-component dosing controls. All known interface options are available for these units for seamless integration. The Maxxis 4/5 weighing controllers are also programmable and can be customised to add functionality.

The BatchPMS PC software is available for the control of complete mixing and filling processes in industry. With the help of this software, the most complex processes can be implemented on the control side and visualised, also, third-party sensors can be integrated. All common industrial interfaces can be used for these weighing electronics and terminals.
Due to its robustness and accuracy, weighing technology is the optimal method for determining the content of bulk materials. In addition, the advantage of dosing is that the conveying speed can be changed without influencing the measured values. This means that the gravimetric method can be used in a wide range of industries, from determining the content of building materials to applications in the agricultural, food and chemical industries and the production of cosmetics.