Temposonics® sensors used in PERRIER Bottling machines
Champagne, the famous sparkling wine from the Champagne region of the same name in France, stands for high quality and good taste. Since every single drop is precious and must not be wasted, champagne producers entrust the production and bottling processes to modern, reliable and highly automated machines. PERRIER Bottling Machines is one of the best-known machinery manufacturers among champagne producers.
In this article, Stephane Chambon, Automation Manager at PERRIER, explains how Temposonics® position sensors optimize the control of bottling machines.
The history of PERRIER begins in 1962, when René Perrier developed his first rotary machine for a French beverage company. It was a mechanical bottle turning machine that managed to turn the bottles upside down with the help of an exclusive handling system with mechanical grippers for gripping the bottles.
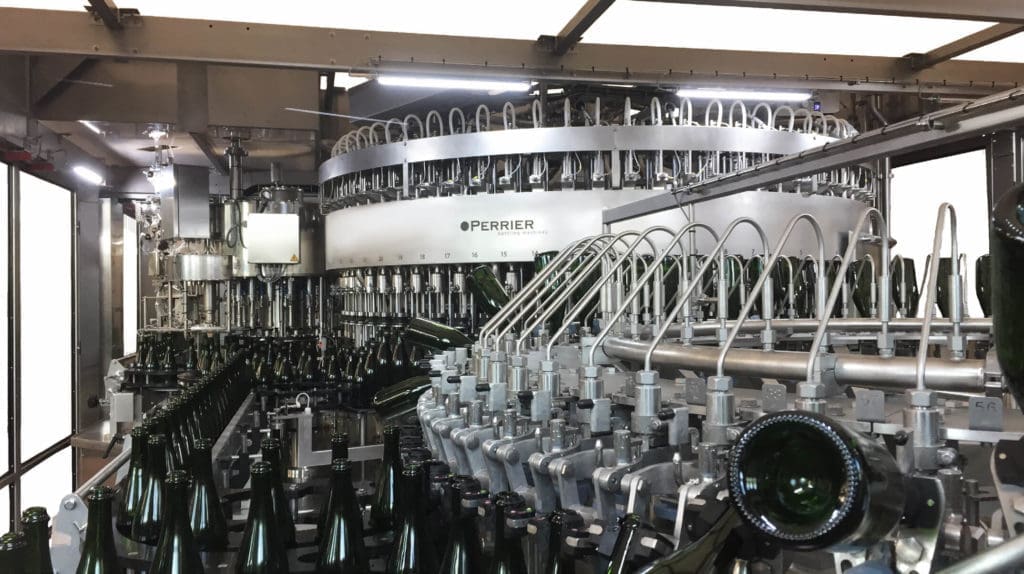
Although the machinery was conceived for the homogenization of lemonade, it was immediately evident that the exclusive mechanism could also be used in the production of champagne. Then, unexpectedly, the champagne sector became PERRIER’s main market.
Furthermore, PERRIER machines are used in almost all sectors of the bottling industry in France: it is almost impossible to imagine the beverage production market without them.
This market dominance alone shows the range of possible uses of the PERRIER product portfolio. At PERRIER, contact and communication with customers is of particular importance.
The systems are designed and built according to customer requirements. “We build custom machines for our customers, so each one is unique,” says Mr. Chambon. A monobloc system, for example, fills and corks bottles.
“The our smallest machines are able to bottle from 6,000 to 8,000 bottles per hour. The bigger ones reach 25,000-30,000 bottles per hour. This is equivalent to around 500 bottles per minute. Everything always depends on what the customer wants. Our machines are designed around this,” explains Mr. Chambon. Another special feature of monoblock systems is that they collect, filter and reuse the rinsing liquid.
This specific monoblock system is designed to fill and cap up to 12,000 bottles and falls within the mediumsized PERRIER machinery segment. In this type of stain, a total of five Temposonics® E-series linear position sensors, model EH, with analog output, guarantee high precision workflows. Temposonics® absolute transducers are based on the manufacturer’s patented magneto restrictive technology and measure locations reliably and without contact.
A non-contact measurement means no mechanical wear of the sensor. Compared to other technologies, Temposonics® sensors have a significantly longer life. “Initially, we installed potentiometers on our machines, however, due to mechanical wear, we had to replace them regularly. Since we started using Temposonics® sensors, we no longer have these problems”. The EH model of the E-series with stainless steel body is perfect for installation in cylinders, thanks to its rod shape. So, how do transducers ensure high-precision processes?
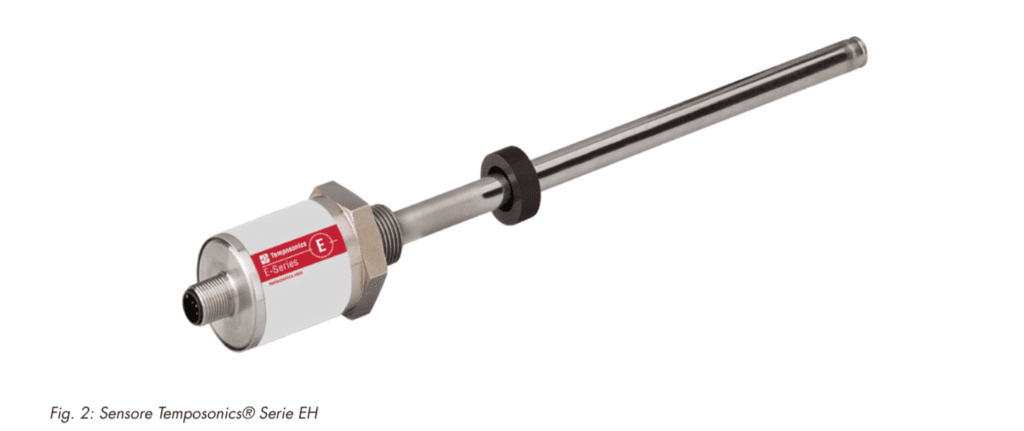
A sensor is located outside the system, where it measures the height of the bottle The information transmitted by the transducers offsets are used to position the filling and capping carousel fully automatically at the correct height. The monobloc system has two tanks. One of them contains the product and the other the rinsing liquid.
The sensors are installed in the tank inside a cylinder, so they do not come into contact with liquids. The exact level is determined with the help of a float equipped with a magnet. Since the contents of the tanks have different densities, it is necessary to choose the right float for each liquid.
Processing large numbers of bottles quickly exposes the sensors to enormous shock and vibration. “With 12,000 bottles filled and corked per hour, the carousels undergo great stress due to the rapid and abrupt movements” explains Mr. Chambon.
Temposonics® position sensors are very durable, maintenance-free and work with extreme precision even in hostile environments, such as a fully loaded monobloc system. Installation is quick and easy. No further sensor calibration is required.
“Since we have been using Temposonics® linear position sensors, our carousels adjust fully automatically and with great precision. Therefore, our machines have become more efficient, cost-effective if and sustainable. Not even a single drop of product is wasted anymore,” enthuses Mr. Chambon.
