After the installation of a new RoRo StretchPack® door packaging line from Tentoma to replace a heat shrink oven, Skantrae has doubled its packaging capacity. Overtime has been eliminated, while both the working environment and packaging quality have been improved.
With a stock of 120.000 doors and an annual sale of more than 600.000 doors, Skantrae is one of the main distributors of doors in in the Netherlands. Skantrae is a Dutch distributor who recent years has had a growth in sales while it also has taken over some operations from a sister company.
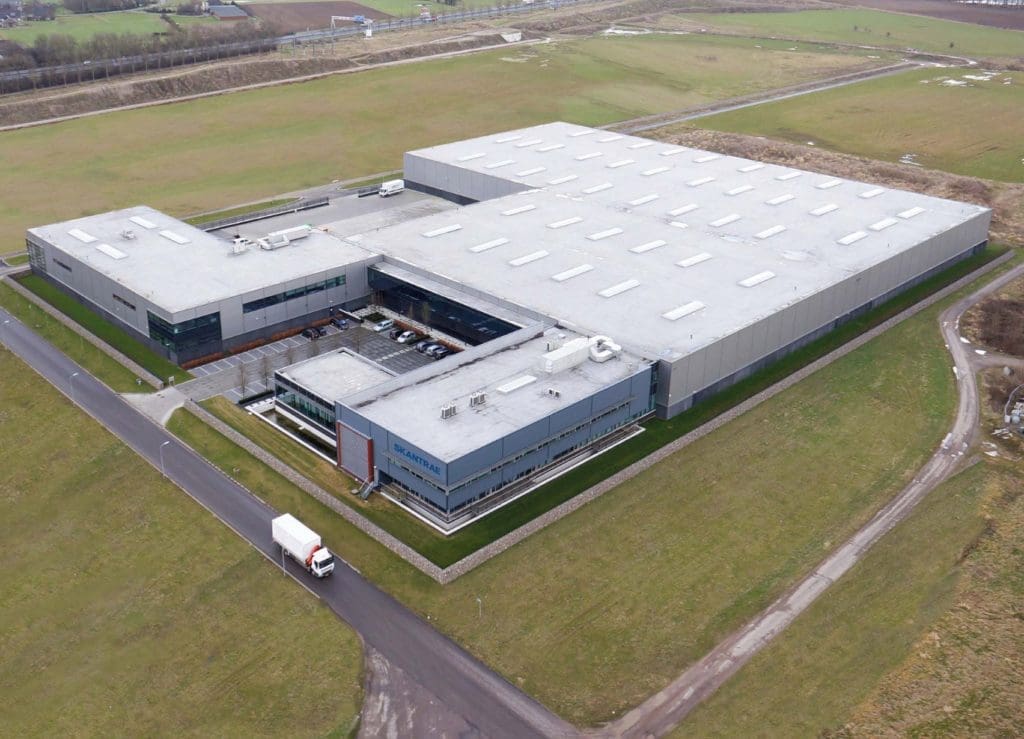

Annual growth in further processing of custom doors on 30- 40% led to a capacity problem on the heat shrink packaging line. That was why operations manager Ruud Willemsen and production manager Peter Klomp, who are responsible for the packaging line, started up a project to find a way of optimizing the packaging.
Peter Klomp tells: “At that time we could only pack 400 to 500 doors each day using the heat shrink tunnel, and that was not sufficient. We needed to pack about 800-900 doors each day, so capacity was the main reason why we were searching for a new packaging solution”.
Ruud Williemsen continues: “Actually, we were looking for a new heat shrink oven. Then we came across the RoRo StretchPack® packaging solution from Tentoma, which we immediately could see was suitable for door packaging. We liked the idea of stretching the film to fit the door instead of applying too much film which we afterwards need to put through a heat shrink tunnel”.
During the project, Skantrae had the chance to do other improvements in connection with the packaging line. Peter Klomp tells: “Previously each door was lifted by hand before packaging when mounting cardboard corner protection on the door. That was about 800 lifts each day.
On the new packaging line from Tentoma we have a lifting table integrated into the infeed conveyor. When the door is placed on the conveyor, we just push a button to lift the door for mounting corner protection. The cardboard for corner protection was redesigned to fit the new packaging line. But actuality, that meant that we could reduce the number of different cardboard sizes from 12 to just 1 size.”

“It was pleasant to work together with the technical staff at Tentoma”, Ruud Willemsen says. “In principle, we were just specifying an ordinary infeed conveyor, when somebody suggested that we should add lifting functionality into the conveyor to lift the doors. For us, it was clear that Tentoma is an engineering-driven company that is open to finding the right solution, which fits our needs. When I think on Tentoma it is with a positive feeling.”
Bas Bosch, who deals with daily operations on the packaging line, confirms that he also has good experiences with technical support from Tentoma after the installation. “It is easy to contact the technical staff directly. If I send them a message with a technical question they usually reply within an hour. Initially, there were some commissioning problems, but Tentoma did some modifications which solved the problems. Every problem is taken seriously, and we have always found a solution. “
30% film savings and improved working environment
Seven months after installation, Skantrae is ready to draw some conclusions from the investment in the new RoRo StretchPack door packaging line. Ruud Willemsen says, “I would estimate that the packaging output has increased with at least 50 to 60 % even with less labour. The old line did 60 doors per hour, and the new line packs for now 90 doors per hour, and we are still increasing that number.
Now we do not have to work overtime in the evening and at the weekend anymore when we need to pack more than five hundred doors per day. “Peter Klomp continues:” To be honest we didn’t see the packaging quality as an issue on the old packaging line, but now when we compared with packaging from the new line, we are proud of the result.
I would estimate that we have achieved film savings of 30% compared to our heat shrink solution.” Besides cost saving, this also reduces the carbon footprint of Skantrae, just like removing heat shrink from the packaging line does.
Bas Bosch and his colleagues in the packaging department state that the new RoRo StretchPack® door packaging line has improved the working environment significantly. In particular, the lifting functionally has been well received, because the work is not so physically hard anymore. Also working next to a heat shrink oven on 160-170 degrees was not a pleasure especially not in the summertime, but that is, fortunately, history now.
Benefits for Skantrae
• Increased packaging capacity on minimum 50-60%
• Reduction in film consumption on approx. 30%
• Removed heat shrink oven from packaging line – less energy consumption
• Improved the working environment – less lifting and no heat from heat shrink oven
• Removed overtime work – less labour costs
• Improved packaging quality
More about Skantrae on www.skantrae.com
