In the food industry, particularly in the meat sector, the person in charge of meat processing plays a key role that is irreplaceable with a fully automated process. This, for instance, happens along the treatment of beef meat, which is difficult to process using robots due to the large volumes of carcasses, making their handling hard.
A process then, which is extremely complex to automate, also for the difficulty of standardization due to the diversity of size, breed, cut of the animal etc. for which, if it were possible to customize the automatic lines in the slaughterhouse, the costs would become unaffordable for any company.
Instead, operators’ skills allow them to recognize meat cuts each time, assess how much fat to separate from the slice of meat, and choose the most valuable cuts or the parts to be discarded as unsuitable.
Highly complex tasks, carried out in wet work environments where it is necessary to employ motorized tools designed to minimize operator fatigue and to facilitate ease of handling and speed of operation in a completely safe environment.
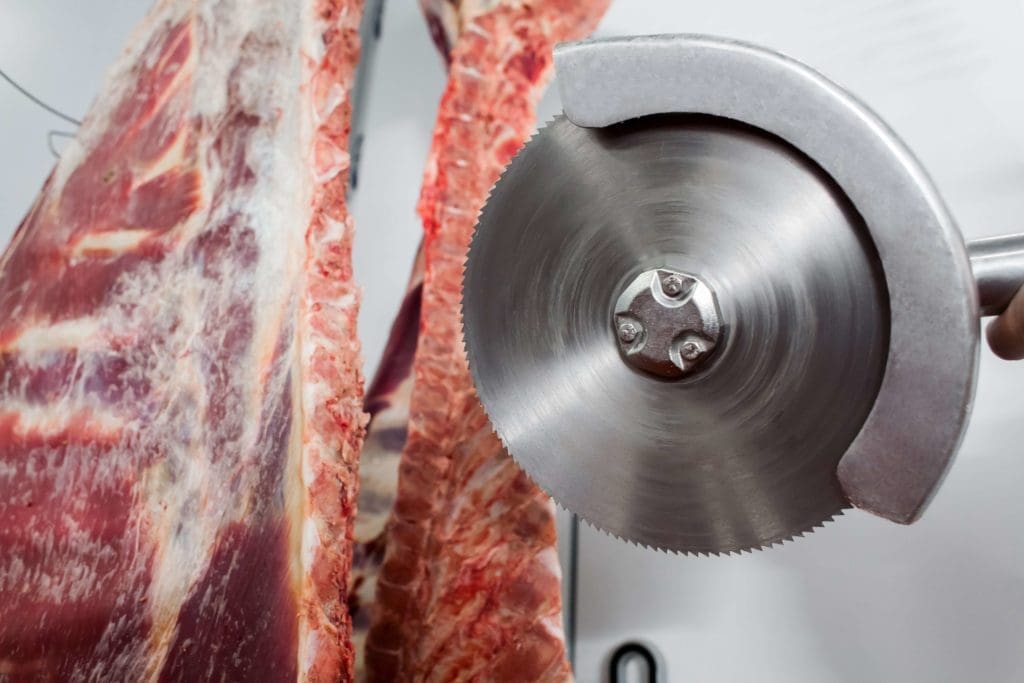
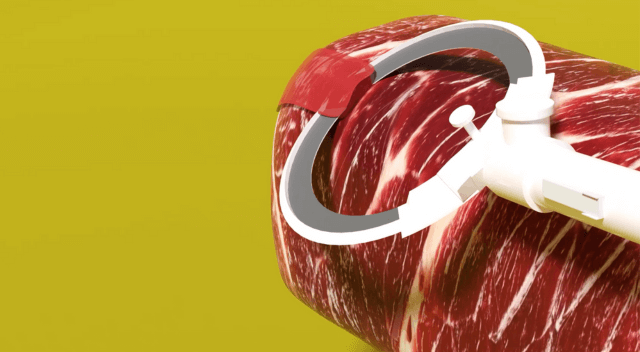
In this area, air technology, compared with electric one, proves to be an optimal choice, with significant benefits not only from a technical point of view but also in operator use, both in terms of safety and convenience.
Infact, air motors made by Fiam integrated as components in meat processing tools have these key features:
• IP67 rating that prevents water/ steam/dust from entering the motor and consequent risk of damage or worse short circuits
• High corrosion resistance due to galvanic that make them highly resistant to aggressive agents
• Fabrication with high-quality stainless steels that meet ISO standards
• Cavity-free outer surfaces that prevent dust and dirt accumulation and ensure ease of cleaning and sterilization
• Gears processed with foodgrade lubricant and internal coatings made with specific treatments to reduce vane friction and increase motor life.
Handheld tools air motors driven so, for the safety aspects related to the constant presence of water and moisture in production sites (driven by cleaning and sterilization requirements), are perfectly compatible with the food industry, as they can be easily cleaned without the risk of a drop in performance or damage to internal components if the tool is not carefully dried.
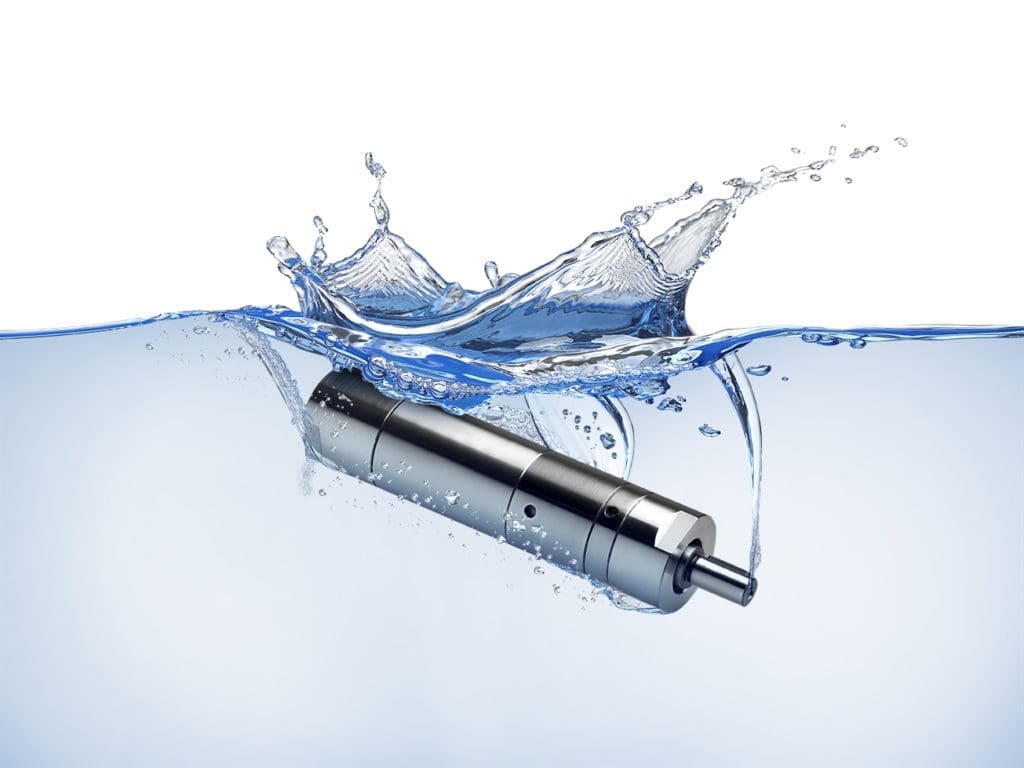

Otherwise, tools with electric motors are extremely delicate, as even the smallest bit of dirt could damage them. This implies scrupulous cleaning activities with very fine drying steps to avert possible short circuits that would irreparably damage the tools, also compromising safety for operators.
Compared to electric motors of equal power, air motors are able to work withstanding repeated starts and stops and, if brought to a shut-down, do not generate any overheating, actually cooling down while running and thus preventing any risk of short-circuiting.
Electric tools, on the other hand, have a greater complexity due to the technology used, which makes them more difficult to repair, more subject to the risk of damage, with higher costs to be incurred not only in maintenance, but also for customization requirements to the applications needed.
Finally, the dimensional factor is decisive for the inclusion of air motors on handheld tools of different types, especially in terms of overall dimensions and weight.
Compared to electric motors, which make handheld tools heavy and bulky, the compactness and low weights of air motors mean in fact that they take up less space, a quarter of an electric motor of equivalent power, and favour their installation on any tool, even the smallest.
Not to mention the low level of vibration transmitted by the motor to the tool and thus to the hand-arm system. This translates into ergonomic advantage for the operator, who can have air tools that reduce fatigue and the risk of “end of shift” injuries, facilitate operations and increase safety in work environments.
