In many countries, the production of bakery goods is one of the largest and fastest growing segments in the food
industry.
Minebea Intec offers a unique range of products and services for the various tasks in this area.
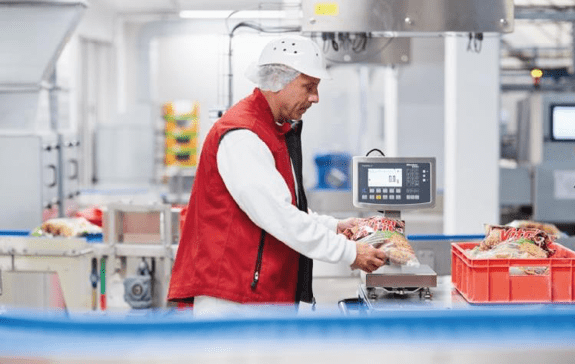
The international food and beverage industry has been experiencing something of a boom in recent years. By 2023, the
annual growth rate is expected to be in the region of 10.3 percent. The industry’s total sales in the three largest markets alone China, the UK and South Korea will be around EUR 34 billion in 2019. In many countries, the production of bakery goods is one of the largest and fastest growing segments in the food industry, and is often only surpassed by sales in meat and poultry production.
The challenges posed by this growing demand include trends like consumers’ desire for healthier, vegan or vegetarian products and the clear labelling of ingredients on packaging. Producers of bakery goods also have to contend with increasing environmental requirements and present their products in a more environmentally conscious manner. Even societal changes like the rise in single person households and increasing mobility affect the industry: packaging sizes and the way that products are prepared change and present growing challenges for producers of food products and bakery goods.
Before the end consumer can buy and enjoy their baked goods, there are a lot of processes to complete, which can roughly be divided into four steps. First, the required raw materials are delivered. The actual production is the second step and is either carried out manually or by automated means. This step is made up of many individual processes, from dosing, mixing and kneading the ingredients to adding them to the moulds for baking, cooling and eventually cutting the baked goods. The products then need to be packaged up, during which various inspections and checkweighing processes are usually carried out. The final step is to dispatch the goods, which involves picking the order and shipping the finished bakery products to retailers or end customers. As one of the leading manufacturers internationally of industrial weighing and inspection technology, Minebea Intec supplies flexible, high performance solutions for each of these sets of processes in the baked goods industry.
Increasing requirements for production technology
With the demand for food growing exponentially worldwide, a much higher level of automation is required in the industry and this includes the production of bakery goods. High precision, reliable technology is needed to inspect the baked goods in virtually every single one of the work steps described above in order to guarant ee the large quantities required at a consistently high level of quality. Silo weighing solutions and floor scales record the exact material quantities during the various production phases and truck scales perform the same task at goods receipt and goods issue. Checkweighers record the product weight for quality assurancepurposes. Metal and X-ray inspection systems ensure during various process stages that the end products do not contain anything other than the desired ingredients. Every component that comes into direct contact with the food must fulfil strict hygienic design requirements to minimise any safety risks for the consumer.
The bakery goods industry is an important customer segment for Minebea Intec. “With our unique portfolio of products and services, we offer a wide range of solutions worldwide for this special market, covering everything from receipt of the raw materials to the finished end product,” explains Willy Sebastian Metzger, Director Marketing, Strategy and Business Development at Minebea Intec.
Reliable X ray inspections with Dymond and Dylight

Metzger describes two examples of the high performance X ray inspection systems currently available from his company: the Dymond and Dylight systems. “The Xray inspection systems in our Dymond series are extremely versatile and are ideal for inspecting packaged bakery goods at the end of the production process, for instance. The systems reliably detect foreign objects in the product and enables hollow spaces to be detected in products and check whether the product contents fill the entire packaging.” Whether the food products are dry or liquid, in cartons, bags or portion packs makes no difference to these systems. To meet the individual requirements of each production line, Minebea Intec offers three different Dymond models with belt widths of 200 mm to 800 mm. Multitrack applications with up to eight tracks are also possible with Dymond.
With Dymond Bulk, Minebea Intec has developed an Xray inspection system for bulk materials that enables raw materials such as vegetables, nuts, dried fruit and grains to be reliably checked for foreign objects of any kind at goods receipt. “The Xray inspection also helps to protect downstream machines, like grinders, by monitoring goods that enter the production process straight from the field, as it were,” Metzger explains.
As a genuine plug and play solution, the Xray inspection system Dylight offers all the functions required to inspect packaged food in a compact unit and is often used as an entry level model for X ray inspections. “Our Dylight system carries out similar tasks to the Dymond models and offers an intuitive solution thanks to its extremely compact design and intuitive, time saving operation,” says Metzger. Dylight models take up just one metre of space in production lines, which makes it easy to incorporate them into existing lines.
Needs based, flexible checkweighing
Packaged bakery goods are checkweighed after the actual production process is complete for quality management purposes, to make sure that the product weight is correct and that the product is complete.
Many bakery goods producers check their products using random samples, which are checkweighed using static scales. One solution that Minebea Intec offers for this task is Combics a series of verifiable industrial bench scales that can be tailored to the required maximum capacities and resolutions. The Combics series also offers a special single workstation solution for the pre-packaging checking of bakery goods, which is particularly useful in smaller scale production processes. Automatic statistics and printouts as well as graphical evaluations on the scale display help users with their day to day tasks. This solution can also be adapted if production is being expanded or integrated into a network solution, such as SPC@Enterprise. Checkweighers are used to ensure 100 percent sample reliability on the packaging line. Their integrated separation systems
make sure that any defective products are removed from the product flow without stopping the production process. They also help to improve production efficiency using the checkweighing data that they collect.

Minebea Intec offers a variety of checkweighers for these tasks. They can be configured in accordance with individual requirements and, if customers have very specific requirements, customised versions can even be produced. Metzger highlights the Flexus an d Essentus product families from Minebea Intec as two series of products that are particularly good in this area: “With Flexus, we are offering users high resolution load cell technology that enables maximum throughput with absolute precision even at high process speeds of up to 2.6 m/s.” The name itself reveals another key strength of these checkweighers from Minebea Intec: their flexibility. This quality is particularly useful when needing to adapt line configurations quickly and easily for transitions be tween products, like when producing new and upcoming products, such as vegan snacks.
“Thanks to its intelligent design, the Flexus enables lines to be converted with minimal effort,” Metzger explains, “the width of the conveyor belt is variable and the height of the system can also be adapted to new conditions very quickly thanks to its adjustable feet. The upper frame structure is even designed to allow additional modules or inspection solutions to be mounted, for instance. What’s more, the checkweigher is designed in accordance with the stringent hygienic design directives of the EHEDG.”
Essentus cost effective checkweigher solutions
The latest addition to the Minebea Intec inspection portfolio is Essentus. This new checkweigher comes with
various options so it can be tailored to individual application profiles, and is therefore ideal for both simple and
demanding applications in the production of bakery goods.
“Essentus is an innovative solution and meets the needs of our customers who have clearly defined requirements for these systems,” Metzger explains. “We are often asked for a simple, inexpensive entry level model that enables reliable, precise check weighing and classification on the packaging line. That’s where the Essentus efficiency, which offers the essential weighing functions, comes in. For customers who require more, the Essentus performance offers a checkweigher with
advanced capabilities.” Metzger reveals that verifiable Essentus variants will be available in the near future. “We will then increase the number of potential applications even further and quite significantly,” he says.
The Essentus performance allows the regulation of upstream filling systems and even in the standard version provides a range of statistics that is more than sufficient for most applications, meeting all requirements for production monitoring and data analysis. The detailed analyses are displayed on the LCD colour graphic display, which can be either fixed or separate from the scale, and allows the storage of up to 100 different products.
Both systems are available in versions for different weight classes: for up to 6kg and for up to 60kg. In addition to their high level of weighing precision and robust design, they are easy and intuitive to use and thanks to the latest generation strain gauge technology, among other things offer maximum reliability.
Innovative software for process optimisation
Besides sophisticated hardware systems designed in accordance with hygiene standards, the related software is another important factor in the production of high quality bakery goods. Minebea Intec has a range of innovative options in its portfolio for producers in this area, too. The statistical process control software SPC@Enterprise helps manufacturers to guarantee product quality, food safety and productivity. The current release of SPC@Enterprise 4.0, offers users a comprehensive tool that combines the logging of samples and automatic in process checks for the food industry. It also enables the efficient networking of various equipment and systems from Minebea Intec and other suppliers, rapid process control thanks to a powerful monitoring program, the easy creation of production and verification statistics, and simple data backup options to minimise the risk of data loss. “SPC@Enterprise is a powerful piece of software for pre-packaging checking and statistical process control. We are constantly updating it and expanding its functionality,” explains Metzger. “Our service customers enjoy the added benefit of automatic updates under their contract.”
Release 3.5 of ProRecipe XT offers bakeries powerful, universal recipe management software that can be used for manual formulation and weighing, as well as automated processes. The software’s simple menu guidance helps to make processes more efficient and reliable, while the comprehensive documentation of the weighing process and a host of reporting options improve transparency in the recipe process. What’s more, the entry of information using bar code readers prevents the potential errors caused by manual entry. Both SPC@Enterprise and ProRecipe XT are able to communicate with ERP and MES systems via flexible interfaces and can therefore be integrated in existing structures and systems. Thanks to their modular design, both software applications can be expanded if users are ramping up production.
A highly diversified partner for the entire product life cycle
Minebea Intec is the perfect partner for producers of bakery goods and system integrators wanting to implement powerful systems thanks to its extensive range of hardware and software products for the baked goods industry and decades of experience in this field. The company offers much more than just standard solutions, as Metzger demonstrates: “In the production of bakery goods, like in the food industry as a whole, many products involve very specific requirements throughout large parts of the production process, such as for product handling. In situations where our standard systems no longer cover these requirements, our Global Solutions Department will advise users, and we will then come up with customer specific solutions that meet all of that user’s specific requirements. It goes without saying that we always observe the stringent hygienic design requirements in all our systems for the bakery goods industry, which ensures simple cleaning
processes, among other things.” Minebea Intec also supports customers during the commissioning process, helping to make sure that production starts on schedule. Minebea Intec promises to make daily life safer. This applies not only to the lives of consumers, but also those of producers.