A brief interview with the IMA team behind the highest speed line with the smallest footprint available on the market
The manufacturing of pressed stock cubes is a market niche where a higher level of efficiency is often required: all the machines in the line have to work together in synergy to ensure maximum productivity.
Today IMA is the only supplier on the market that can single-handedly offer a complete line. We had a brief conversation with IMA experts regarding the latest development in this field: a complete line with an output of 2,000 tablets/ minute.
Let’s start with Fabriano Ferrini, Product Manager for Tablet Presses at IMA Active. Since we are talking about pressed stock cubes, I suppose everything starts with a tablet press. Is that right?
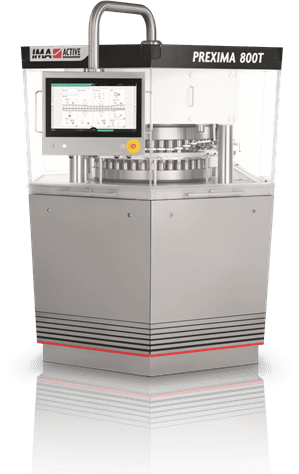
Yes, that’s right: the first machine in the line is a tablet press. Prexima is designed to guarantee high efficiency in production, mainly pursuing two factors: high output and consistent processing. Prexima features several technical solutions for high-speed tableting of bouillon powder.
A new die feeder has been designed specifically for high efficiency feeding of wet masses with low flowability. This has proven to ensure low deviation in weight, even with tablets of 10 grams or more. Compaction and dwell time are also important factors when high speed needs to be reached.
They allow more time for the ejection of the air contained in the powder blend and for the bonds to be made between the particles. Here, the 250 mm pre and main compression rollers mounted on Prexima really make all the difference, as well as the IMA 32T tooling, which features a larger punch head.
In addition, the Prexima high-yield motorisation minimises heat production in the lower compartment, being the ideal solution for low melting or heat sensitive products. Low temperature tableting maintains blend flowability at die feeding, prevents product sticking to punches, and dies and preserves tablet quality.
So, Prexima can run fast. But to achieve efficiency you must ensure a consistent process as well.
Correct: an optimal OEE is based on a robust operation, which minimizes unexpected line stop, reduces cleaning times and maintenance work. From this perspective, Prexima ensures complete separation between processing and mechanical areas thanks to the use of purposely designed seals and protections.
The absence of products in the mechanical area makes for extended duration of cams, tooling and compression rollers, leading to reduced cleaning time.
In addition, a powder-free mechanical area allows for a totally automated and recirculated lubrication system: the control system automatically takes care of lubrication frequency, without any need for operator intervention. In that way, the best parameters do not depend on the operator’s skills. The only required action is to check the oil level and refill it, if necessary.
Now the tablets have to be wrapped. Let’s turn to Davide Giordano, Sales Manager at IMA Corazza.

That is correct. Stock cubes are wrapped by the I20 wrapping machine, in side-folding execution, with its fully electronic operations. The machine can be equipped with the “easy-opening unit” which enables an easier consumer-oriented opening of the stock cube wrap.
The I20 is also able to handle paper-based packaging materials, which is certainly a plus for Corazza solutions in a world where recyclability and sustainability have become a must.
What are the I20’s main hallmarks?
The I20 has been engineered with a very compact footprint, delivering a space-saving solution. What’s more, its modular design means it is easy to access and maintain. Its two-lane execution, equipped with a unique wrapping reel without any aligning unit, ensures gentle operations and high efficiency.
The dedicated feeding system allows for a compact design to be delivered for both the press and the wrapper: products coming out of the pressing unit accumulate on the two-lane conveyor, distanced thanks to the acceleration wheels and then driven towards the folding wheel by a pusher.
The new welding system, installed in the outfeed grouping unit, ensures excellent sealing quality of the final product. Compared to other wrapping equipment available on the market today, the I20 machine concept and operations allow for very fragile products to be handled.
What about maintenance and cleaning?
Since the I20 has been developed to meet customer expectations in terms of maintenance, the plug-in design of the main groups greatly facilitates activities such as reel change, foil feeding set-up as well as infeed and outfeed group cleaning.
The I20 shows its customer-oriented approach through the HMI control panel, which reports machine performances to monitor production, has alarms to tackle downtimes and enables remote machine assistance.
The high number of tablets released by the I20 means an automated solution is necessary to place them into a tray. Let’s listen to Michele Nomi, Area Sales Manager at IMA GIMA, who can give us some more details on the FTB569 tray packer.
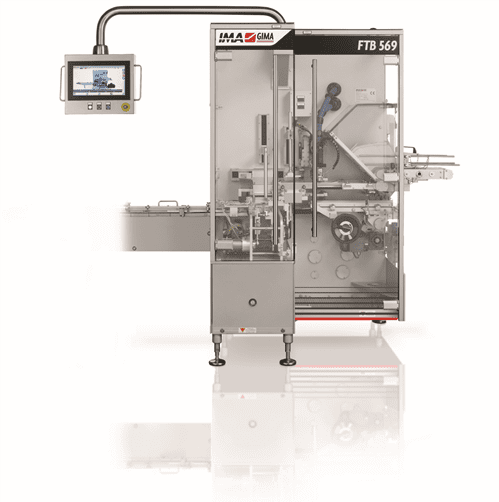
Over the last few years we have seen increasingly faster wrapping machines and, at the same time, a general growth in labour costs. These factors have led many customers to look for automatized solutions also in the end-of-line sector, replacing what was normally done by semi-automatic equipment or even manually by operators.
It has been almost ten years since we began collaborating with IMA Corazza, supplying a downstream wrap-around tray packer for wrapping machines, and I can definitely say it is highly appreciated on the market for its many features. First, its compactness – a total length of approximately 2 metres, including infeed and outfeed conveyors – and its accessibility.
Then, product handling and flexibility: thanks to the servo driven movements and other tailored devices, we can guarantee the smoothest product handling without any damage. Lastly, the machine is designed to provide a quick size change, switching from one format to another by replacing just a few parts, allowing our customers to be reactive to market changes and trends, while maintaining high efficiency levels.
You mentioned the wrap-around tray packer. What are the advantages of this technology?
The fully automatic technologies used to place the tablet in trays are usually top loader and wrap-around. Although we have both of them in our portfolio, for this specific application we have decided to use the wrap-around solution because of several advantages.
Firstly, as we have just mentioned, the compactness of the machine. Secondly, optimised tray dimensions: by forming the tray directly around the bundle, we can design it with zero tolerance between product and tray, which means a reduction in the used material, while achieving significant annual savings in logistic and shipping costs. Last but not least, the quality: a tray that perfectly fits around the product looks better on the shelf and facilitates its wrapping.
Now we should wrap the tray… Let’s ask Enrico Pazzi, Food Sales Manager at IMA BFB, which has a long tradition of designing and manufacturing end-of-line machines, ranging from overwrapping and stretch wrapping to case packing, palletizing and handling solutions. If you had to choose the best machine to end this line, which one would you propose?
The A50: it is a very compact machine. Its reduced footprint also makes it the ideal end-of-line solution when it comes to wrapping because it can easily adapt to any space constraint. Being the final equipment in the line means that it has to be flexible in size if you want it to fit into any space.
The machine is also extremely easy to operate. Operators do not have to be trained or particularly skilled to use it.
We can say that it is designed with the operator in mind because it is easily accessible thanks to its balcony structure: it is very easy to reach the product flow areas for cleaning. The A50 guarantees maximum protection both for the operator and the product.
How is overwrapping carried out on the machine? How is the final quality of the wrap guaranteed?
The machine has specific film unwinding, cutting and sealing systems to ensure that the film is always cut with a very precise fold and sealed without wrinkles, air bubbles or other imperfections. The product is treated with care, lifted by the elevator, gently wrapped and pushed to the sealing area, where it is securely sealed and closed as it goes through the sealing plates.
Thanks to this system, the machine can handle very thin films, like 16 micron films, considering the standard thickness is 22-24 micron. The option of handling thinner films brings significant advantages because, on the one hand, you can reduce the cost of the packaging material and on the other, you have a greater film reel autonomy which means less operator intervention.
Make the most
The IMA Virtual event dedicated to Confectionery and Snack market
The Sensing Future Days cycle continues: a new virtual event completely dedicated to the processing & packaging solutions for the Confectionery market will take place on May 27th, the agenda will be available in the next days. Join the Sensing Future Days community to receive updates on the agenda.
March edition: the last virtual event entirely dedicated to complete lines for stock cubes, processed cheese, butter & margarine, yoghurt, beverages & baby food and of process technologies for gums, candies & coated sweets is now available on-demand on the IMA Sensing Future Days Platform. Sign-up now at sensingfuture.ima.it to re-watch these sessions, as well as any other session from past editions.