Any industrial process and production environment is only as effective as the reliability of its equipment. The failure of any component within the process line can be responsible for unscheduled repair windows, which can have a serious financial and reputational cost to the operator. In food, beverage, and dairy product manufacturing and processing, the risk factor is multiplied. Any degradation of the equipment can lead to product contamination, impacting not only the business but the health of consumers.
The choice of material for sealing systems is often overlooked in terms of importance to process line reliability. The inexpensiveness of seals relative to other components can lead reliability engineers to assume a correlation to the importance of seals, but this could not be further from the truth.
An incorrectly specified sealing material can break down quickly, causing seal failure and resultant equipment failure – with the associated cost of batch contamination and lost production. Understanding the particular demands of a food process environment and how that should inform material selection is a key concern for operational reliability.
The Perlast range of FFKM sealing materials – exclusively manufactured by Precision Polymer Engineering (PPE) – has been engineered specifically for this market, to deliver exceptional reliability and unrivalled sealing performance in the most challenging of process environments. FFKM is the sealing material you use when failure is simply not an option.
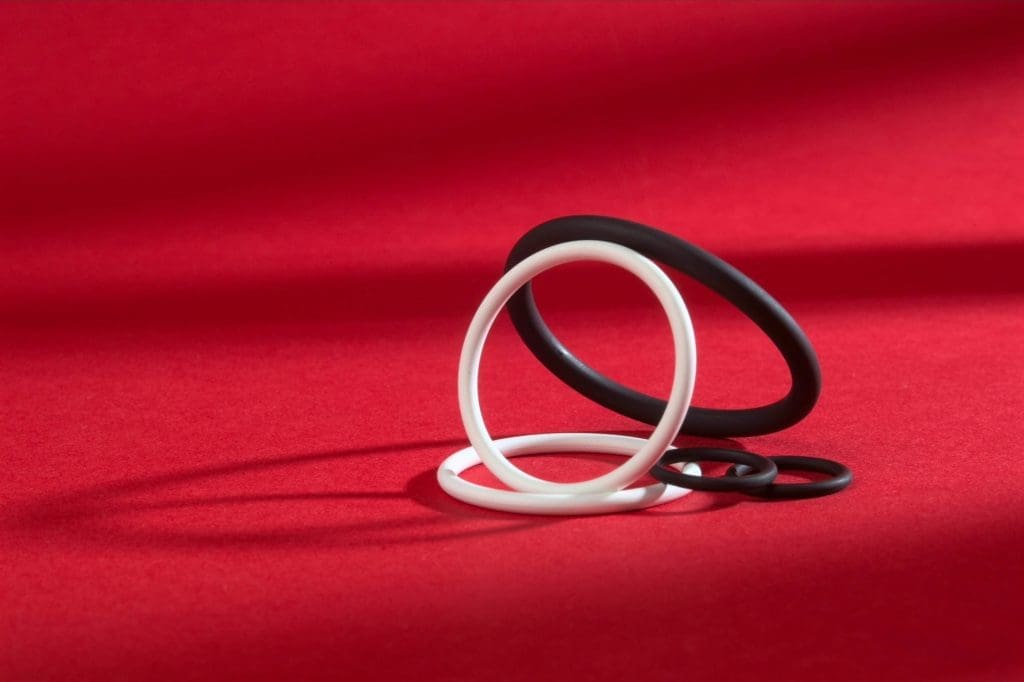
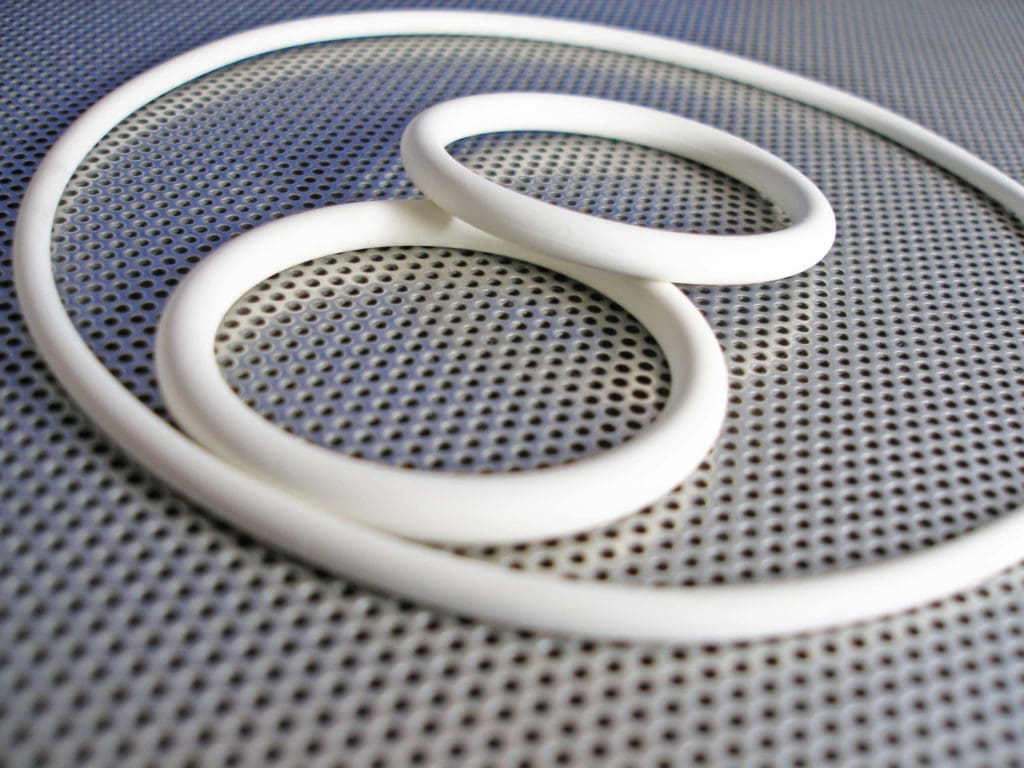
Engineering confidence in challenging sealing environments
The environments faced by elastomer seals in food production can be particularly aggressive. Processes can involve substantial thermal fluctuations, and exposure to harsh chemicals – both in terms of the process media, but also in Clean-in-Place (CIP) and Steam-in-Place (SIP) cleaning and sterilisation regimes. This variability in conditions is a cause for concern in many operations, as what is a strong performing material in one environment may become a liability in another. The search for across-the-board compatibility with chemicals and thermal environments has led food industry leaders to Perlast.
Perlast is an FFKM material which is engineered for long term reliability and performance in the most critical food process environments. In high temperature testing, Perlast material grades retain excellent sealing capabilities up in temperatures up to 260°C, as well as sub-zero applications.
The molecular structure of Perlast is very similar to PTFE, featuring a unique cross-linking system which ensures compatibility with virtually all chemicals, across a full range of acids, amines, alkalis, and alcohols. This enables users to rationalize onto a single material grade across all applications. Beyond thermal and chemical properties, Perlast material grades are prized for their mechanical properties, performing well in test and in situ for static and dynamic applications, demonstrating good compression set and abrasion resistance.
The ability for food process operators to rely on Perlast seals to perform long term without degradation or failure – whatever conditions their processes might throw at them – is hugely beneficial. The reduced lifetime cost of ownership is a major advantage, with the reassuring knowledge that one Perlast seal will outlast several seals made from a competitor material grade. Production can continue without interruption from unscheduled MRO. Supply chain complexity is reduced, saving logistical headaches. There is also the invaluable peace of mind which comes from the security of sealing with a material with no thermal or chemical weaknesses.
Introducing Perlast G74S
Material scientists and specialist sealing engineers at PPE are always hard at work developing new technologies to support the work of life science applications. In recent months, Precision Polymer Engineering introduced Perlast G74S – a step change in sealing for food and beverage applications.
Perlast G74S is a white perfluoroelastomer (FFKM) combining the universal chemical resistance and high temperature capability demanded by the food and beverage industries. One vitally important element of sealing in life science industries is the strict adherence to all relevant industry standards. When it comes to food safety, there is no room for compromise.
Perlast G74S is compliant with the following standards:
- Food & Drug Administration (FDA)
- USP Class VI (chapters 87 & 88)
- 3A 18-03 Sanitary Standards (class I)
- EC1935/2004 and EC2023/2006
The performance characteristics of Perlast® G74S are substantiated by stringent data collected from PPE’s purpose-built test laboratory. Key testing capabilities rang from chemical compatibility and failure analysis through to thermo-mechanical evaluation and detailed microscopy.
The right material and the right profile
Getting the correct material is only half the story. Effective sealing performance – particularly in food production – is also determined by identifying the optimal profile design for the requirements of the application. PPE is currently supplying Perlast grades into food, dairy, and water applications as O-rings, HyClamp sanitary gaskets, D-seals, IDF seals, SMS 1149 seals, and diaphragms. but by offering a custom component design service, PPE can engineer Perlast sealing components to the exact requirements of a specific application.
PPE has over 30 years’ experience in food grade rubber manufacturing to the European Hygienic Equipment Design Group (EHEDG) guidelines. These guidelines look beyond the seal material and consider the seal in its operating environment. PPE routinely uses Finite Element Analysis (FEA) simulation techniques to develop hygienic seals which do not pose a contamination risk through their potential to ‘trap’ particles or bacteria.
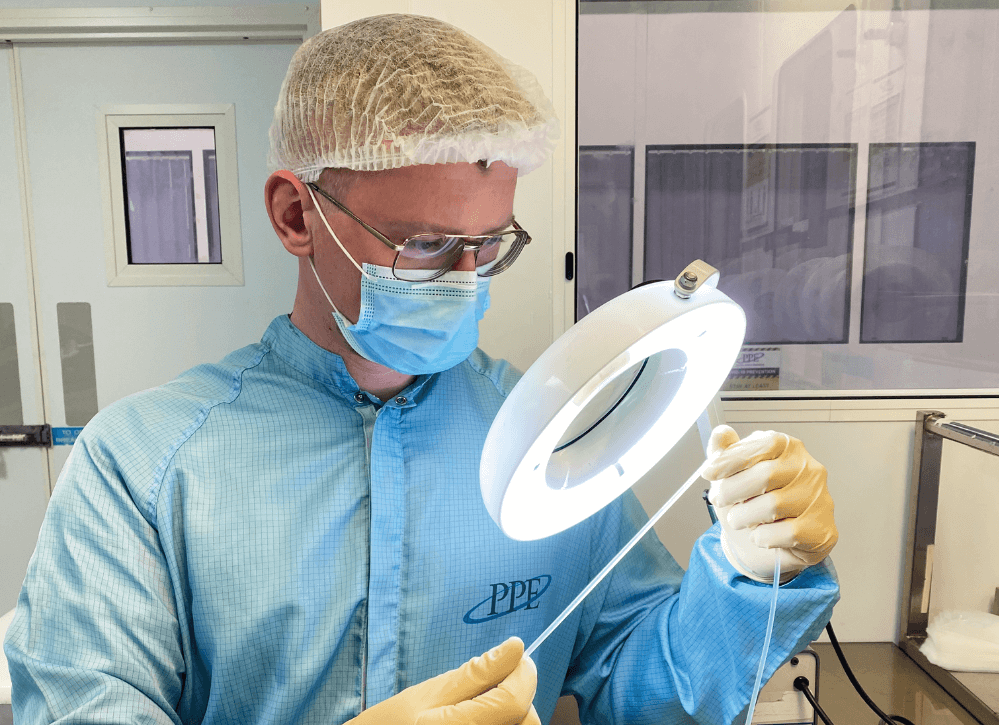

With you every step of the way
PPE goes beyond simply manufacturing sealing products. There is a focus on the provision of comprehensive support from experienced specialists, made available through the lifetime of the product. There is a sense of pride at PPE in being a full service partner for all elements of critical sealing. The wealth of experience and expertise across teams of specialist engineers and material scientists is all geared towards keeping the customer’s operational downtime to an absolute minimum.
From the first consultation, PPE’s team of sealing specialists seek to build a collaborative relationship. It is only by fostering this deep level of teamwork that PPE can gain a deep understanding of the challenges of the application, and all parties can work towards the development of a Perlast sealing solution which exceeds performance expectations. Combining the specification and implementation of an upgraded sealing solution with ongoing long term aftercare as a trusted sealing partner, PPE customers can feel confident that their operations are safeguarded against the severe consequences of seal failure.
Through a framework of ongoing technical support from specialists with an understanding of the industry, leaning on the responsiveness of a global network of technical channel partners, Perlast users enjoy a lifetime of bespoke sealing support to keep their operations running efficiently.
Specifying a new FFKM material – why now?
PPE sealing specialists understand the difficulties of specifying a new FFKM material. However, there is a reason why many food and beverage process lines are choosing this moment to specify Perlast in their sealing upgrades. The global availability of FFKM is poor, due to supply chain disruption caused by export embargos on key ingredients, and continued fallout from the Covid pandemic. This scarcity has led to lead times of up to six months for some major seal companies, and while some operators have sought FFKM alternatives in FKM and EPDM, the suitability is just not the same.
With Perlast FFKM, seals can be supplied to order in as little as 30 days. It means that operations aren’t compromised by FFKM availability and unacceptable lead times for sealing components, keeping process lines moving, with high productivity and low running costs. Crucially, it also means that food production companies don’t need to compromise on material suitability, and gamble with the safety of their end consumers.
Next steps?

Perlast FFKM seals combine outstanding high temperature resistance, almost universal chemical resistance, and excellent mechanical performance. If you would like to enquire about test samples of Perlast for qualification, or if you have any questions about the suitability of Perlast for your application or industry, visit www.perlast.com.