Revised machine design, higher performance and smaller footprint address industry’s most pressing needs, while delivering contemporary performance and integration capabilities to wider markets
A two-year development program for a packaging solution with an outstanding 30-year pedigree has resulted in a new range of Sleever machines from leading global packaging technology company Cama Group.
The three new machines in the range offer better speed, simpler integration, a smaller footprint and significantly improved flexibility – all of which are coupled to a servo-based infrastructure and a digital architecture that will deliver seamless Industry 4.0 integration.
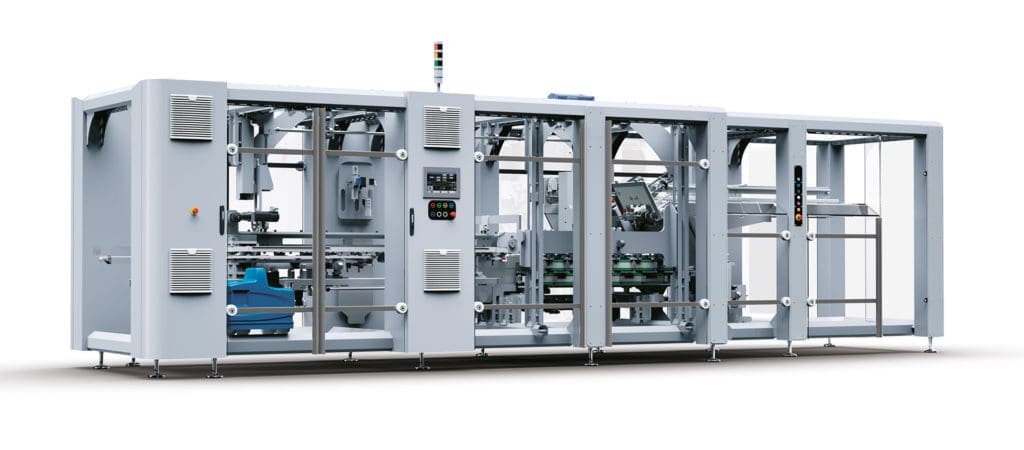
“Sleever machines have been part of our product offering for the last 30 years,” explains Alessandro Rocca, Group Sales Director at Cama. “They have always offered impressive speed and performance, but we knew we needed to develop them further to make them more suitable for modern connected plant operations.
“The market for this machine technology is growing,” Rocca explains. “We have always enjoyed successes in the dairy industry, but we are starting to see a real pull from other verticals, such as pet food and ready meals – both of which would benefit from this newer technology.”
There are multiple facets to the redevelopment of the machines. First is a new framework, based around the company’s class leading Breakthrough Generation (BTG) approach.
This comprises a modular, scalable design that offers easy entry and access, optimized cable runs and hygienic features, all of which house contemporary automation solutions – including advanced rotary and linear servo technology and robotics – to deliver the all-important flexibility and adaptability required by modern packaging operations.
“We have also redeveloped the primary internal elements,” Rocca adds, “such as the rotary feeder, which is not only faster, but comprises fewer parts, which will result in greater uptime and far easier maintenance.
We have also simplified the infeed starwheel and clamping system for the same reasons.” A new phasing device has also been deployed, which phases one or two-layer configurations accurately.
This double-pitch layout will give users the flexibility to more easily adapt the machine depending on the packaging format required, and this is coupled to a new stacking device at the infeed for the creation of double layers.
The new designs also cater for packaging variety. “One of the important enhancements is the ability to deploy a corrugated cardboard overwrap for larger product arrays,” Rocca explains. “Sometimes compact cardboard is simply not up to the job, so we offer the possibility of stronger packaging with a stronger closure.”
The starwheel, the phasing device, the rotary feeder and the stacking device are all smaller than the technology they replace, which has resulted in a machine that is overall smaller/ shorter – an essential design cue, especially for plants within limited or premium real estate. “We also like to make the machines easier to operate,” Rocca enthuses.
“Not only does the new design benefit from our simpler clamp-based format changeover – with single- to double-pitch conversions taking less than 20 minutes – but we have also lowered the blank magazine, making it far easier to load.”
Tight integration of Cama’s in-house-developed robots allows users to create multi-flavour configuration, insert gadgets or leaflets and formulate multiple stacks. “In a standard application we may see the same cup design, but in different layer counts,” Rocca adds.
“However, for different product arrays – that could be multi flavour or require the insertion of a sachet, spoon or leaflet – robotics is certainly the way forwards, as the immense flexibility offered by our robots removes the need for large-scale format changes.
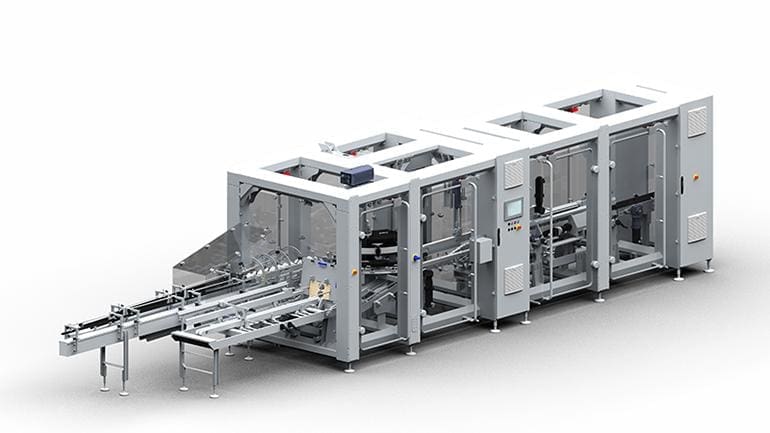
“We can also integrate case-packing,” Rocca adds. “Most of the time, the products go into trays, which is typical for dairy, and we have developed a case packer that is 100% integrated onto the sleeving machine, even removing the need for conveyors or other phasing units.”
Available in three variants depending on the complexity and requirements of the application, the new MP series – like other new variants in Cama’s extensive packaging technology range – will set the standard for the industry. Already in action at a leading global dairy company, the machines have proven their pedigree.
“We really do feel that we can now offer the complete package to all of our customers in all the industries we serve,” Rocca concludes. “With full Industry 4.0 compatibility, seamless robotic integration, multi-architecture control solutions and the services of our highly experienced packaging design team, we have customers returning time and again.
And with extensive AR and VR capabilities – including completely immersive customer design reviews and flythroughs before a contract has even been signed – it’s not just our machine performance that makes us the first point of contact.”