The performance of end-of-line packaging systems plays a key role in ensuring an efficient production, capable of quickly adapting to market changes and improving the quality and sustainability of the final packaging of beverages, food, detergents and chemical products.
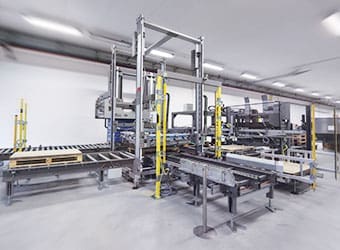
SMI automatic palletizing systems from the APS ERGON range represent the ideal solution for managing an uninterrupted, optimized and flexible production flow, capable of quickly switching from one format to another, according to the consumers’ purchasing habits.
An example of this flexible technology is represented by the APS 4140 L ERGON palletizer, which stands out for the perfect synchronization between pallet loading, palletizing layer formation and interlayer insertion.
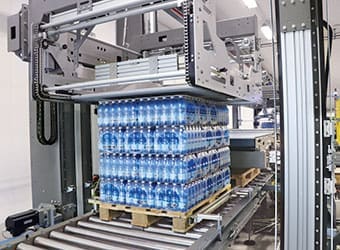
The new palletizer designed by SMI is a high-performance system equipped with two independent columns that perform the vertical movement for palletizing boxes, bundles, trays and packs in general with a production speed up to 140 packs per minute / 400 layers per hour (values can change according to the product): the first column is equipped with motorized belt, while the second with basket.
Moreover, the APS system is composed of pre-wired modules that can be configured on an individual basis, with advantages in terms of easy and quick installation and start-up, as well as versatility and capacity to adapt to any end-of-line logistic condition.
Operation of the system
An innovative system for the pack rotation and/or continuous handling carries out the layer pre-formation: the bundles arriving on the single-lane conveyor are turned, moved and arranged on more lanes according to the palletizing pattern.
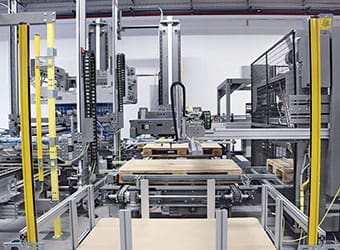
The first column receives the complete layer from the infeed module and, moving on the vertical axis, brings the product to the height of the basket of the second column; from here, through the motorized belt, the layer is inserted into the basket that deposits it on the pallet. At the end of this operation, the basket, moving on the vertical axis, moves to the waiting position of the next layer.
Main advantages:
–very compact infeed with continuous preformation, which optimizes the end-of-line spaces
-layer formation system equipped with rounded, sliding protection doors in anodized aluminium
-versatile system composed of pre-wired modules that can be configured in a customized way, in order to adapt to any logistic end-of-line condition
-high operational flexibility with the possibility to realize several palletizing patterns
-ICOS motors equipped with integrated digital servo-driver with low energy consumption
–door closure system with deceleration device
–ergonomic and functional structure of the frame, which simplifies the plant maintenance operations for the operator
-accident prevention protections in aluminium and polished polycarbonate (PC)
-palletizing patterns optimized for the truck loading
–minimized format changeover times
-product smooth movement that avoids damages during handling
-innovative design solutions in IoT key
–simple and intuitive control of all operations

For further information please contact our sales department or visit our web site.
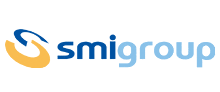