MGM Motori Elettrici is the leader in brake motor technology, manufactured in Italy and consolidating its reputation and presence in the market for over 70 years in Europe and in the World.
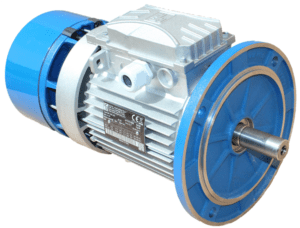
MGM Motori Elettrici’s facilities in Italy include the main production plant in Serravalle Pistoiese (Pistoia) and a warehouse with commercial offices in Assago (Milan). Further plants in Montreal (Canada), Detroit (USA), Chennai (India) and Izmir (Turkey) complete a global presence further enhanced by a network of distributors for sales and assistance in more than 70 countries.
The success of our AC brake motors is owed to the ingenuity of an innovative design created in our laboratories. With great ambition, three years ago we set out to further upgrade our brake motors.
The first step was to discuss and receive feedback from consultations with over 100 technical departments at our customer sites around the world. With focus on the features and improvements they would like to find in their ideal brake motor.
Our goals were not only to meet the recommendations provided by our customers but even to extend the life cycle of our motors, to increase the average energy efficiency and to give priority to the use of recyclable material with low environmental impact.
Since 2008, the average amount of energy our products need to operate has steadily decreased. In addition, by rethinking and redesigning materials and the production process, we have reduced the energy needed for the manufacture of our brake motors with a significant reduction of the greenhouse gas emissions. We felt it appropriate to speed up this process.

All single-speed motors are already available with the level of energy efficiency in accordance with the new European regulation that has entered into force since July 1st 2021, the brake coils are undergoing improvements in terms of reducing energy consumption and increasing performance.
Motors with IEC frame sizes 100 and 112 will be the first to be presented in the market with most of the planned upgrades.
The dimensions compared to the current production will be reduced, the frame offers an optimal heat dissipation capacity and allows, thanks to two dedicated lifting eyes, greater ease of handling.
The terminal board has been made more accessible, simplifying the connection and reducing the installation time for the benefit of the end user. We then designed and realized, by patenting it, a new methodology that allows us to use rotors with larger active parts for the benefit of efficiency but without increasing the moment of inertia of the motor.
All this has allowed us to improve the dynamics and maintain the capacity of a huge number of starts per hour. The remainder of the motor frame sizes will receive the same improvements during this year.
For MGM Motori Elettrici sustainable development and respect for the environment have always been very important goals.
In the Serravalle Pistoiese plant almost 100% of the electricity consumed is produced by the photovoltaic panels placed on the roof, the air conditioning is supported by a geothermal system and the consumption of drinking water has been reduced.
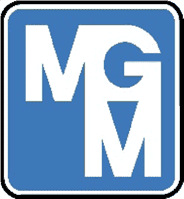