Con un approccio personalizzato alla manutenzione, possiamo prevedere la durata di un sistema e sapere quando è necessario effettuare la manutenzione preventiva.
Di Roger Savo, Direttore Aftermarket Europa di ELGi
Nell’ambiente industriale odierno, caratterizzato da ritmi frenetici e in cui i tempi di inattività equivalgono a significative perdite finanziarie e inefficienze operative, l’implementazione della manutenzione predittiva e preventiva (PPM) è diventata non solo un’opzione, ma una necessità per le aziende di tutti i settori.
Questa strategia integrata non solo migliora l’affidabilità e le prestazioni delle apparecchiature, ma ne prolunga anche la vita operativa, assicurando efficienza e durata delle operazioni industriali in un modo che sottolinea l’efficacia dei costi.
Che cos’è la manutenzione predittiva e quali sono i suoi componenti chiave?
La manutenzione predittiva è una strategia di manutenzione avanzata che sfrutta l’analisi dei dati, l’apprendimento automatico e le tecnologie dei sensori per prevedere e prevenire i guasti alle apparecchiature prima che si verifichino.
A differenza degli approcci tradizionali alla manutenzione, come la manutenzione reattiva (che risolve i problemi dopo che si sono verificati) o la manutenzione preventiva (manutenzione programmata indipendentemente dalle condizioni dell’apparecchiatura), la manutenzione predittiva si concentra sulle intuizioni basate sui dati per ottimizzare i programmi di manutenzione e massimizzare i tempi di attività e l’affidabilità delle apparecchiature.
Le nuove tecnologie connesse svolgono un ruolo cruciale nel favorire l’efficienza della manutenzione predittiva. Integrando sensori e reti con strumenti di analisi e intelligenza aumentata, i sistemi di manutenzione predittiva possono offrire previsioni più accurate e approfondimenti in tempo reale.
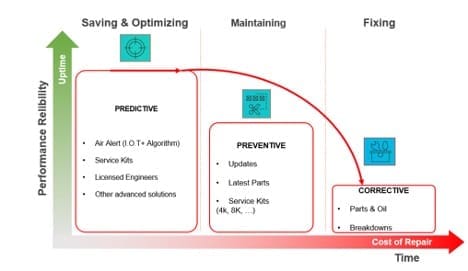
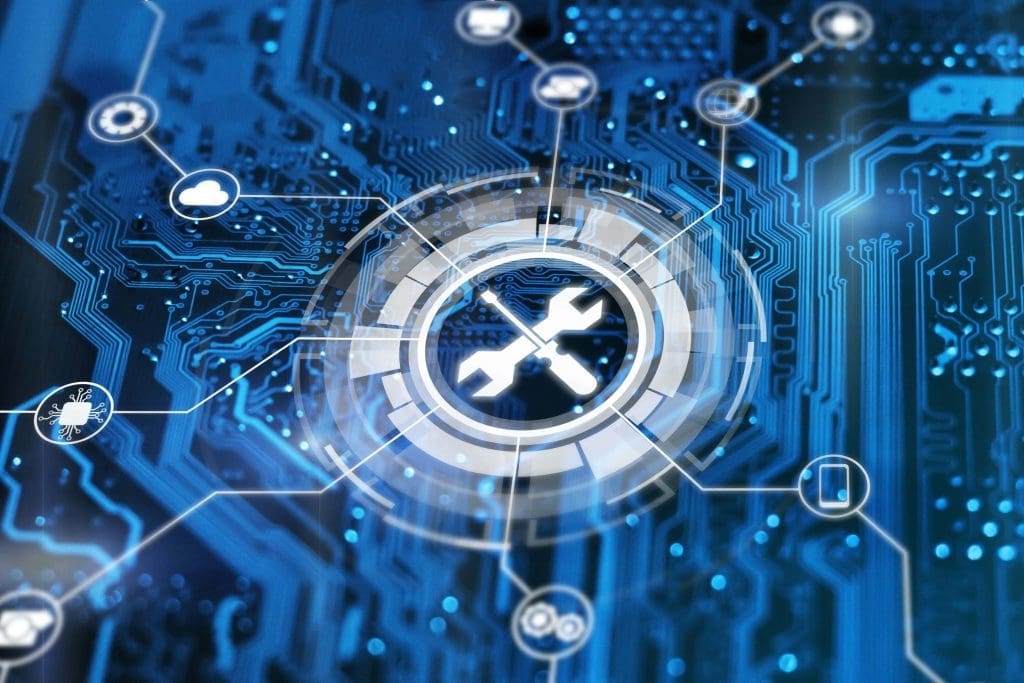
Dispositivi di comuncazione
Air~Alert di ELGi è un sistema intelligente di monitoraggio e allarme remoto delle macchine basato sull’IoT, attivo 24 ore su 24 e 7 giorni su 7, che può essere implementato su impianti nuovi ed esistenti. Il servizio consente ai clienti di agire in tempo per evitare potenziali guasti ai compressori, grazie al monitoraggio remoto 24/7 di un sistema di aria compressa.
A tal fine, fornisce grafici di tendenza e informazioni sui parametri operativi, tra cui la pressione di mandata, la temperatura dell’olio, la velocità del convertitore di frequenza variabile (VFD), le ore di funzionamento totali, gli interventi e gli avvisi su un’interfaccia online accessibile in remoto da qualsiasi parte del mondo.
Air~Alert funziona anche come sistema di manutenzione predittiva, notificando ai clienti ed ai Channel Partners ELGi la manutenzione programmata, l’insorgere di anomalie e prevedendo i guasti più comuni. I rapporti mensili di riepilogo sullo stato generale e sui parametri di funzionamento includono i requisiti di assistenza programmata e la manutenzione preventiva basata sui dati del sistema.
Le integrazioni tecnologiche intelligenti consentono un’agilità “alwayson”, in cui le condizioni impreviste dei macchinari possono essere affrontate tempestivamente, riducendo così i danni potenziali e ottimizzando i processi decisionali. La connettività facilita uno scambio di dati completo, migliorando l’analisi predittiva e consentendo decisioni strategiche e precise sulla manutenzione degli asset.
Componenti chiave dei sistemi di manutenzione predittiva e preventiva (PPM):
L’implementazione della manutenzione preventiva richiede un approccio strategico, sostenuto da diversi componenti chiave:
• Tecnologia avanzata dei sensori: I sensori IoT sono fondamentali per il monitoraggio in tempo reale delle condizioni delle apparecchiature, fornendo i dati necessari per l’analisi predittiva.
• Analisi dei dati e intelligenza artificiale (AI): Il cuore del PPM risiede nell’analisi dei dati e negli algoritmi di intelligenza artificiale che elaborano i dati raccolti dai sensori per identificare modelli, prevedere potenziali guasti e suggerire misure preventive.
• Manodopera qualificata: Una forza lavoro esperta nell’analisi dei dati, nell’apprendimento automatico e nel funzionamento di sofisticate apparecchiature di monitoraggio è essenziale per interpretare i dati e implementare efficacemente le strategie di manutenzione.
• Cambiamento culturale: L’adozione del PPM richiede un cambiamento culturale all’interno dell’organizzazione, passando da una mentalità di manutenzione reattiva a una proattiva. Questo passaggio comporta formazione, gestione del cambiamento e assistenza continua.


Come funziona la manutenzione predittiva:
Il processo di manutenzione predittiva si svolge in diverse fasi:
1. Raccolta dati: Monitoraggio continuo e acquisizione di dati dai macchinari.
2. Analisi dei dati: Applicazione di tecniche statistiche e di apprendimento automatico per analizzare i dati raccolti.
3. Rilevamento delle anomalie: Identificazione di modelli di dati che si discostano dalla norma, indicando potenziali problemi.
4. Previsione e processo decisionale: Uso di algoritmi predittivi per prevedere i guasti e decidere le azioni di manutenzione.
5. Manutenzione proattiva: Esecuzione delle attività di manutenzione prima che si verifichino i guasti, sulla base di intuizioni predittive.
Vantaggi dell’implementazione della metodologia PPM:
La motivazione per l’adozione della metodologia di manutenzione predittiva e preventiva all’interno delle attività aziendali è sottolineata dai suoi significativi vantaggi per le imprese:
- Riduzione dei tempi di inattività: I tempi di inattività non programmati sono un danno per la produttività. L’adozione della manutenzione predittiva è stata collegata ad una significativa riduzione dei tempi di inattività non pianificati, migliorando la produttività complessiva.
Le tecnologie connesse facilitano il processo di manutenzione predittiva, consentendo approfondimenti in tempo reale e l’impiego efficiente delle risorse di manutenzione. Secondo Deloitte Analytics Institute Position Paper on Predictive Maintenancequesta efficienza si traduce in una riduzione del 20-50% dei tempi di pianificazione della manutenzione, in un aumento del 10- 20% dei tempi di attività delle apparecchiature e in una riduzione del 5-10% dei costi complessivi di manutenzione.
In particolare, l’implementazione della manutenzione predittiva in settori come la produzione chimica e i trasporti ha portato a una significativa riduzione dei tempi di inattività e dei costi di manutenzione; un grande produttore chimico ha ottenuto una riduzione dell’80% dei tempi di inattività non pianificati e un risparmio di circa 300.000 dollari per asset.
2. Riduzione dei costi: Il PPM riduce significativamente i costi di manutenzione identificando i problemi prima che si trasformino in costose riparazioni o sostituzioni complete delle apparecchiature. Ottimizzando i programmi di manutenzione, le aziende possono evitare attività di manutenzione non necessarie, risparmiando su manodopera e ricambi. Secondo Advanced Technology Services (ATS), la manutenzione predittiva consente di risparmiare dall’8% al 12% rispetto alla manutenzione preventiva e fino al 40% rispetto alla manutenzione reattiva. Questo dato sottolinea i vantaggi finanziari dell’adozione di strategie di manutenzione predittiva rispetto agli approcci tradizionali.
3. Estensione della vita dell’apparecchiatura: Una manutenzione regolare e precisa prolunga la vita operativa dei macchinari. Secondo una ricerca di McKinsey, la manutenzione predittiva può ridurre i tempi di fermo macchina del 30-50% e aumentare la durata della macchina del 20-40%. Questo dimostra l’impatto significativo che le strategie di manutenzione predittiva possono avere sull’estensione della durata operativa dei macchinari, consentendo alle aziende di rinviare le spese di capitale per le nuove attrezzature e di ottimizzare il ritorno sugli investimenti per i beni esistenti.
4. Maggiore sicurezza e conformità. L’implementazione di strategie di PPM può migliorare significativamente la sicurezza sul posto di lavoro e garantire la conformità alle norme di sicurezza. Identificando e risolvendo in modo proattivo i potenziali guasti alle apparecchiature prima che si verifichino, il PPM riduce al minimo i rischi di incidenti, creando un ambiente più sicuro per i dipendenti. Questo approccio proattivo non solo protegge la forza lavoro, ma aiuta anche le aziende a rispettare i rigorosi standard di sicurezza, evitando così le sanzioni legali e finanziarie associate alla non conformità.
5. Efficienza operativa: Con il PPM, le aziende beneficiano di un aumento generale dell’efficienza operativa. Se i dati vengono raccolti ed analizzati correttamente e le attività di manutenzione vengono eseguite in tempo, l’usura delle apparecchiature si riduce, migliorandone le prestazioni.
Conclusioni
L’implementazione della manutenzione predittiva e preventiva non è solo una best practice, ma un imperativo strategico per le aziende che mirano a prosperare nel panorama competitivo e in rapida evoluzione dell’Industria 4.0. Adottando il PPM, le aziende possono ottenere non solo significativi risparmi sui costi e guadagni di efficienza, ma anche migliorare la loro resilienza operativa. In un’epoca in cui i tempi di inattività possono rappresentare una battuta d’arresto critica e si cerca continuamente di aumentare l’efficienza, il PPM si pone come faro dell’eccellenza operativa, assicurando che le aziende rimangano agili, proattive e in anticipo rispetto ai potenziali fallimenti.
