Global flexible packaging and lidding films supplier KM Packaging has launched a new range of mono-polymer material lidding films, made from polypropylene (PP), that is designed for recyclability. The sustainable films seal and peel to PP and PE-lined PP trays and can be used during microwave cooking as well as being suitable for ambient, chilled, or frozen applications.
Part of KM’s K Peel range, it allows food manufacturers to meet the growing demand, particularly from supermarkets, for mono material packaging that is designed for recycling.
The lidding films are ideal for the packaging of poultry, meat, and chilled prepared foods. Features include:
• Mono structure made of one material type.
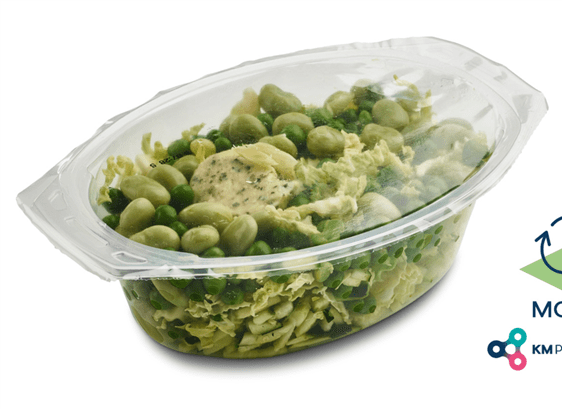
• Designed for recyclability.
• Ideal for use during food preparation and microwave cooking.
• Peelable from the tray.
• Suitable for ambient, chilled, or frozen applications.
• Exceptional transparency.
• Excellent anti-fog capability.
• Available with or without barrier.
As well as satisfying the needs of supermarkets and consumers who are seeking more recycle-ready solutions, KM is helping to future-proof its food packaging. KM Packaging’s commercial director Graham Holding explained: “If you have a piece of flexible packaging that, for example, is a combination of paper, plastic, and aluminium foil, then that would be a really difficult thing to segregate and put into a recycling stream.
“It is anticipated that the UK government’s Extended Packaging Producer responsibility regulations, due in 2023, will quite highly penalize packaging like this that is difficult to recycle.” The new PP lidding film is also designed for recycling around the world, with some countries already having well-developed recycling infrastructures for polyolefin (polyethylene and polypropylene) plastics. In the UK, front-of-store recycling facilities allow consumers to return polyolefin-based flexible packaging.
A similar approach is taken in other markets. For example, Australia’s REDcycle initiative and, in South Africa, polyolefin are the largest plastic commodity recycled by weight. Therefore, putting a tray/film combination of polypropylene onto the market feeds into an already well-established recycling system.
And the new “Designing for a Circular Economy” guidelines from CEFLEX focus on polyolefin-based flexible packaging. This is due to the material making up an estimated 70-80% of the flexible packaging waste stream and because the ability to sort and mechanically recycle it is already proven at an industrial scale in Europe.
KM Packaging’s main purpose is to “protect, present, preserve”.
That is delivering the best packaging solutions by:
• Protecting products throughout the entire process, from factory to tabl
• Presenting food in a way that is attractive, professional, and recognizable.
• Preserving food and extending shelf-life across the food industry
Graham said: “The main goal of our packaging is to look after and protect food. We don’t compromise on that. But we’re also trying to make sure it’s designed for recyclability and, when appropriate, it’s thinner and lighter. These are big drivers in our product-development process.”
The new polypropylene lidding film products follow KM’s recent launch of all-polyester (PET), weld-seal, mono-material lidding films within its K Seal range. Both solutions are designed for recyclability and will allow customers to avoid putting multi-layer trays and films with different plastics combined into the market.