Responsibility of manufacturer and critical issues.
Before explaining what is needed to purify compressed air in the food and beverage industries, it is first necessary to understand the regulations and standards imposed on manufacturers and retailers in the sector. Non-compliance is not an option.
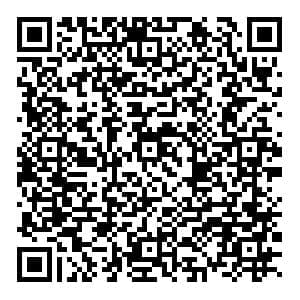
Hygiene legislation requires food and beverage manufacturers to instigate a written Food Safety Management System based upon the principle of HACCP (Hazard Analysis Critical Control Points). Is mandatory that manufacturing company must ensure that the preparation, transformation, manufacturing, packaging, storage, transport, distribution, handling, sale or supply, including the administration of food products, are carried out in a hygienic way.
To provide a more auditable means of implementing HACCP procedures, many companies are adopting standards such as ISO22000:2005 that fully endorses the principles of the HACCP system. Conducting a hazard analysis will assist in organising the knowledge required to establish an effective combination of control measures.
Normally, the HACCP procedure is strictly applied to the main production processes However, due to lack of awareness, it is not always applied or properly applied for utilities. The most overlooked energy source in a manufacturing plant is compressed air which powers many manufacturing processes/applications and is often used in direct or indirect food contact but at potential risk of contamination. This is a major issue; Compressed air directly or indirectly in contact with machinery, equipment, products and packaging can unknowingly contaminate them.


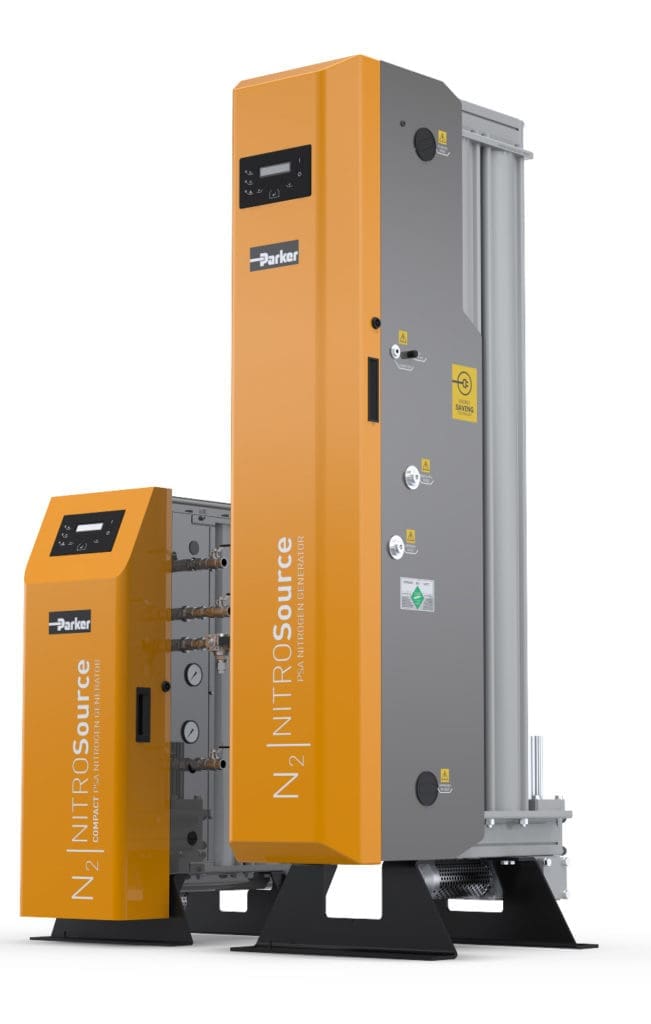
Which correct guideline must be followed for the of compressed air in contact with food?
The British Compressed Air Society (BCAS) has created a code of practice (Food Grade Compressed Air Code of Practice) to be followed for the correct treatment of compressed air at every point of use. It is the only GMP “safety program” tool, recognized internationally, which provides detailed specifications regarding the use of HACCP and the relative grade of quality of the compressed air to be respected both for direct contact and indirect.
Parker is a member of BCAS. Every point in a food industry plant, where compressed air is used, is classified as a CCP (Critical Control Point) due to the contamination present in the compressed air system and adequate measures must be taken to reduce the contaminants present in compressed air at acceptable levels.
To define the quality standards of compressed air to be adopted in direct or indirect contact with food, the BCAS refers to the regulation that regulates air quality ISO8573-1:2010. The BCAS indicates that the air in direct or indirect contact (but with potential risk of contamination) with food, before a sterilizing filter, must have a purity quality in accordance with classes 1.2.1 dictated by the international ISO8573:1-2010.
Parker Solutions to ensure certified quality gas in contact with food & beverage.
There are different purification technologies to remove contaminants in a compressed air system: coalescing filters, refrigeration and adsorption dryers, solid particulate filters and sterilizing filter. It is necessary to guarantee and demonstrate to the inspection bodies that the air in contact with food is clean, dry (water vapor with a pdp value -40°C) and sterile (free of microorganisms and bacteria) to prevent contaminants from compromising the food safety and hygiene. Before a sterilizing filter, according to the BCAS code of conduct and ISO standards, it is necessary to reach the ISO 1.2.1 classes dictated by the ISO8573:1- 2010 standard.
It is highly recommended to treat all compressed air in the compressor room, with a refrigerated dryer and filters, to protect the main distribution system, and to supply high quality air with a dedicated drying system only at the point of use” critic”.
This approach at the design level guarantees correct air treatment and represents the most convenient solution for having high quality compressed air, as shown in the example layout below.
Parker offers dedicated filters and dryer certified for the market like the new complete FPB “Food, Beverage & Pharma” purification system dedicated to the food and beverage industry.
FBP integrates all the necessary purification technologies in a single compact skid for the removal of most contaminants thanks to 6 purification stages. CERTIFIED outlet air guarantee. Performance of the filters and dryer certified by the third-party validating body “Llyods Register” to provide air quality as standard in accordance with ISO85873-1 classes 1.2.0 Filters tested according to ISO12500-1 and ISO8573-5, dryers tested according to ISO7183.
Parker Filters and Dryers are designed to provide compressed air quality that meets or exceeds the standards set out in all revisions of the ISO8573-1 “International Air Quality Standard” and the standards of the Code of Conduct for the use of BCAS compressed air for food use.
The performance of Parker products is certified by Validating Third-Party Bodies and furthermore the filters and dryers are manufactured with:
Construction materials compliant with FDA Title 21 part 77 and exempt from EC1935-2004 regulation. These peculiarities make Parker products for compressed air treatment the perfect purification system for the food and beverage industry.
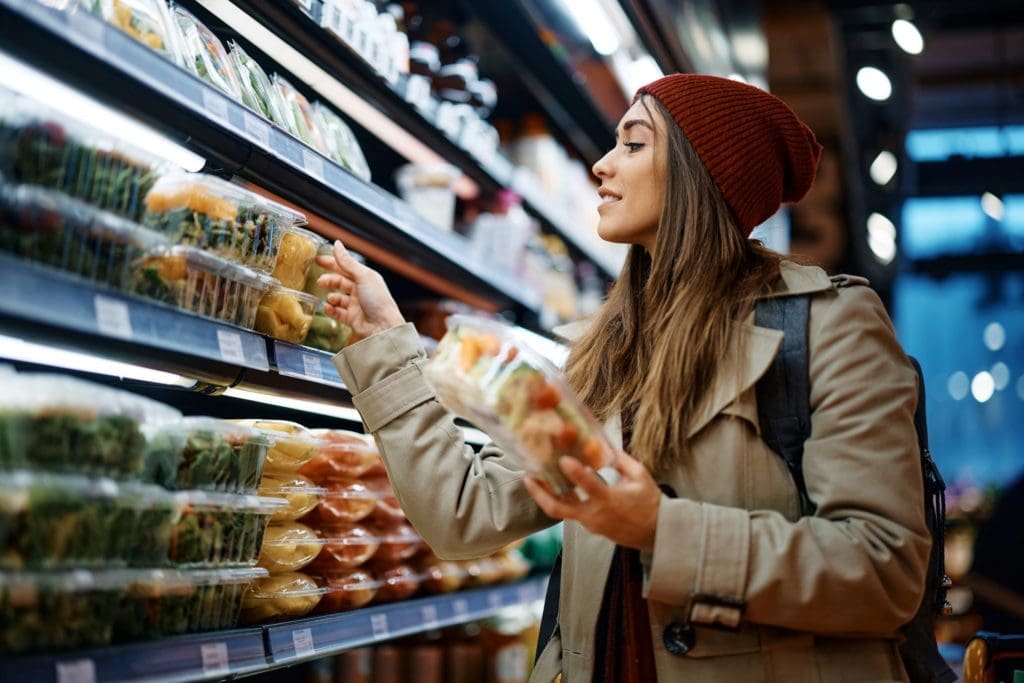

Not only compressed air but also food grade nitrogen!
In addition to the quality, flavor and appearance of the food, the quality of the nitrogen used in the packaging or inerting phases is also of fundamental importance.
Specification requirements for gases used in MAP applications vary by country. For example, in Europe, EIGA has developed a specification that indicates the maximum level of contaminants that is considered acceptable in food grade gases.
Nitrogen is classified as a food additive when it comes into direct contact with food. In this case it is indicated by the letter “E” followed by a number. The nomenclature for nitrogen is “E941”. In the European Union, compliance with the specified contamination levels is mandatory by law.
Parker thanks to NITROSOURCE PSA offers nitrogen generation systems to obtain nitrogen of purity certified by an Independent Validating Body to obtain nitrogen of suitable quality for use in contact with food.
