Citrus packhouses are striving to meet evermore demanding quality expectations, yet must also increase quantities and improve yields. This is a tricky balancing act, but it can be done, as Clinton Jeffries, Global Category Director Citrus at TOMRA Food, explains.
The fact that consumers are getting choosier about citrus fruits is having consequences for packhouses. Whatever the citrus variety, the risk is the same: if the fruit disappoints the buyer, the food brand or retailer that sold it could lose future sales. This means that retailers increasingly expect their suppliers to provide perfection – not easy for packhouses because incoming fruit is variable and outgoing fruit has to satisfy so many requirements.
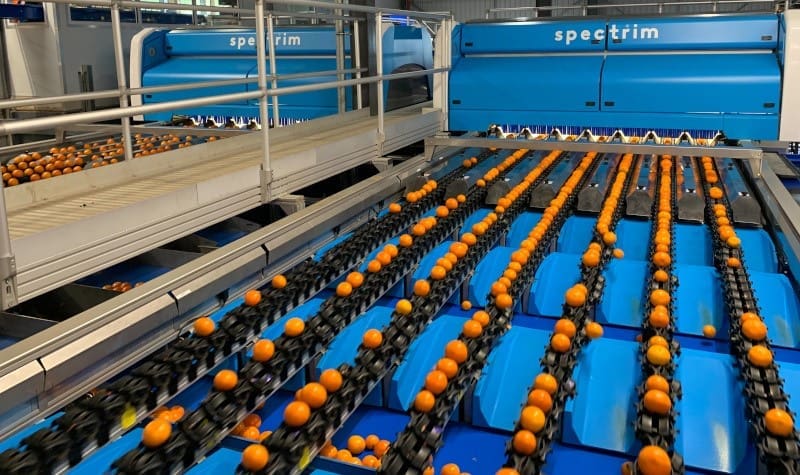
To start with, the fruit’s skin condition, color, shape, and size all affect shelf appeal. Then the eating experience can depend on the fruit’s firmness, texture, and sugar content. And to complicate things even further, consumer preferences about fruit color and sweetness differ from one export market to another.
Packhouses have traditionally kept their customers happy by packing only the fruit they are sure will meet quality requirements and by rejecting fruit of borderline quality. But this too often leads to fruit ‘giveaway’ which hurts packhouse profits. More money could be made if the packhouse finds a way to deliver the required product quality and quantity while simultaneously maximizing yields: a balancing act that demands precision.
As packers tread this tightrope, the stakes are dizzyingly high. Global exports alone are worth more than $7 billion annually – and rising. In established markets, more consumers turn to healthy, natural, vitamin-rich foods, making citrus fruits more popular. In emerging markets, growing numbers of people are earning middle-class incomes and spending more on food. And greater use is being made of citrus fruits for flavoring and coloring in bakery products and fruit beverages. For these reasons, citrus sales are expected to keep rising in value at a compound annual growth rate of 4% so that by 2030 exports will be worth about $10 billion.
This does not mean, however, that increasing packhouse profitability will be plain sailing. In fact, the industry faces headwinds.
Facing up to future challenges
For growers, perhaps the strongest headwind is climate change, causing greater seasonal variations in crop yields and quality. In many regions, there’s also the threat of citrus greening (also known as HLB or Yellow Dragon Disease), which turns the fruit bitter and kills infected trees within a few years. In the early 2000s, HLB famously devastated many citrus farms in Florida, and the disease wiped out millions of acres of citrus trees throughout the world.
Proactive countermeasures can be effective, but these require constant vigilance, reduce yields, and increase costs. For packers and re-packers, the headwinds are also coming from different directions. While quality expectations are rising, the increasing variability of crops is pulling in the opposite direction. Sorting and grading the fruit well is vital, yet every year it is getting harder to recruit and retain people to do this. And the costs of labor, energy, and other essential resources are climbing, intensifying the need to maximize yields and profits. It’s now more important than ever to put the right fruit into the right package at the right time.
For retailers, there’s an increasing need to differentiate through product quality. With consumers getting pickier, export markets will only pay top dollar for top quality. Retailers are also under increasing pressure from consumers to take sustainability seriously. This requires, among other things, an active approach to reducing food waste – another obligation that gets passed on to packhouses.
The good news is that packhouses can power through these headwinds. Answers to many of today’s packing challenges are provided by state-of-the-art optical sorting and grading machines. These automated solutions are far more accurate and consistent than manual sorting and grading. They enable packhouses to meet required standards, regardless of incoming fruit quality. They open doors to new customers with high-quality requirements. And they bring an end to the costly habit of fruit giveaway.
The best available solutions
The leading manufacturer of optical sorting and grading machines for the food industry is TOMRA Food. The unmatched effectiveness of TOMRA’s solutions results from the company’s significant ongoing investment in research and development, a deep-rooted culture of innovation, and decades of working closely with food processors and packers, which has led to a deep understanding of their unique operational challenges. TOMRA sees customer relationships as a collaborative process involving processors and packers in designing new solutions.
In the citrus industry, TOMRA’s solutions are in action in the USA, Europe, Australia, South Africa, North Africa, South America, and Asia. In California alone, the company typically installs up to 200 new lanes at citrus packhouses yearly. Yet despite being active globally, the company focuses on providing best-in-class customer support at the regional level. And though TOMRA provides solutions to the industry’s biggest players – including the world’s largest citrus packhouse operation, which has more than 200 lanes – it also works with many small businesses with just one or two lanes.
Three TOMRA solutions are well-suited to citrus fruits: the Spectrim sorter and grader, long recognized as the standard-setter in blemish-grading vision systems; Inspectra², a non-invasive solution for internal grading; and the fruit industry’s most advanced sorting platform, the TOMRA 5S Advanced.
Sorters and graders tailored to citrus
The Spectrim sorter and grader is the world’s most powerful fresh produce grading platform, with consistent lighting, powerful imaging, two infrared wavelengths, and machine learning. Spectrim sorts and grades minor and major defects, including surface blemishes, insect damage, misshapen fruit, bruising, and abrasions, and can identify hard-to-find product defects, including clear rot.
Sorting parameters can be configured to grade for differing levels of defects, giving line operators the control to match product grades to different markets. Many packhouses around the world benefit every day from using Spectrim. One of these is Agricola Cerro Prieto, which exports fruit globally from Peru. The company’s Operations Manager, Ricardo Acha, said: “Technology is of the utmost importance to us, and thanks to the constant advances [made by TOMRA], we can process bigger volumes. With Spectrim, our volumes have almost doubled.”
The Inspectra² platform for internal defect grading utilizes a near-infrared spectrometer, mainly to to detect brix, but also to provide valuable information about other properties important to citrus growers and packers. These detection capabilities keep bad fruit out of a good box, ensure fruit with the preferred taste profile goes to the right market, and help growers adjust their practices in the field to optimize internal fruit quality.
“Spectrim and Inspectra² have opened up new opportunities, especially the brix grading with Inspectra²,” says Pieter Nortje, owner of the Sitrusrand citrus farm, which stretches 60 kilometers along the Sundays River Valley in Eastern Cape, South Africa. “With Spectrim, you get very good quality sorting and there is very little machine downtime, so you also get consistency on delivery. The TOMRA machines are critical in putting the right fruit in the right carton with the right traceability system.”
The TOMRA 5S Advanced, launched in 2021, builds on the class-leading performance of the Compac Multi-Lane Sorter (TOMRA acquired Compac in 2016), but was redesigned from the ground up. In addition to inspecting with unrivaled accuracy, this is the industry’s gentlest-handling fruit sorter, and exceptionally easy to clean and maintain. This machine’s specialized software – with programs for element mixing, exact packout optimization, and throughput control – provides optimization and efficiency across the line. All these features can be controlled easily via the sorter’s intuitive graphic user interface.
The TOMRA 5S Advanced also features a Dynamic Lane Balancer which ensures equal fruit distribution across all lanes of the sorter. Requiring no operator input, this constantly makes automatic adjustments informed by data from its interface with the Sizer software. Without a Dynamic Lane Balancer, almost every machine will have lower cup fill on the outside lanes; with it, there are significant throughput increases on the same number of lanes when compared to other systems.
One of the many processors that has seen the TOMRA 5S Advanced improve productivity, as well as product quality, is leading Turkish citrus exporter Özler Tarim. The company’s General Manager, Özbek Özler, said: “We predicted that we could invest in our second [TOMRA 5S] machine after two or three years, depending on the results achieved by the first machine. But we were so satisfied that we ordered our second machine just three months later. Thanks to investing in TOMRA’s technologies, we doubled the capacity of Özler Tarim, which has a 35-year history, in just one year.”
Combining two machines can have the effect of “one plus one adding up to more than two”, in the experience of Chinese citrus fruit producer Xiangjia Juyou. Hunan-based business installed two TOMRA six-lane sorting and packing lines in 2021 in pursuit of raising productivity to 100,000 tons of citrus annually and targeting products to markets with differing quality expectations. Jia Kaijun, Director of the fruit Department at Xiangjia Juyo, affirmed: “Externally, the fruit is assessed according to color, defects, and peel blemish caused by diseases and insects. Internally, the fruit is sorted by brix and acidity. This precise sorting enables targeted sales strategies.”
The future looks bright
Another state-of-the-art technical solution that unlocks efficiency improvements is the cloud-based data platform TOMRA Insight. First introduced to processing and packing lines in other food
categories, this is expected to be rolled out to citrus packhouses within the next couple of seasons and has the potential to make sorting machines the digital heart of processing and packing operations.
One advantage of the machine data accessed by TOMRA Insight is that it opens a pathway to traceability from bin to pack. Another is that machine operators can respond easily and instantly to live data to improve line efficiencies. And another is that analysis of historical data can lead to yet more efficiency gains on the line and in the supply of raw materials. Packhouses which rely on hard data, rather than merely experience and instinct, make better-informed operational and strategic decisions. This, like the best sorting and grading solutions, strengthens the packhouse’s competitiveness – and powers progress even when there are headwinds.
About TOMRA Food
TOMRA Food designs and manufactures sensor-based sorting machines and integrated post-harvest solutions transforming global food production to maximize food safety and minimize food loss, by making sure Every Resource Counts.
The company has more than 12,800 units installed at food growers, packers and processors around the world for Confectionery, Fruit, Dried fruit, Grains and Seeds, Potatoes, Proteins, Nuts, and Vegetables.
These solutions include advanced grading, sorting, peeling and analytical technology to help businesses improve returns, gain operational efficiencies, and ensure a safe food supply.
TOMRA Food operates centers of excellence, regional offices and manufacturing locations within the United States, Europe, South America, Asia, Africa and Australasia.
Follow TOMRA Food on Facebook @TOMRA.Food, Twitter @TOMRAFood, Instagram @TOMRAFood and on LinkedIn at TOMRA Food.
TOMRA Food is a division of TOMRA Group. TOMRA was founded in 1972 that began with the design, manufacturing and sale of reverse vending machines (RVMs) for automated collection of used beverage containers.
Today, TOMRA is leading the resource revolution to transform how the planet’s resources are obtained, used and reused to enable a world without waste. The company’s other business divisions comprise TOMRA Recycling, TOMRA Mining and TOMRA Collection.
TOMRA has approximately 100,000 installations in over 80 markets worldwide and had total revenues of ~10.9 billion NOK in 2021. The Group employs ~4,600 globally and is publicly listed on the Oslo Stock Exchange. The company headquarters are in Asker, Norway.
