A leading American dairy products company, which supplies retail, food service and co-manufacturing, with products including natural, processed and speciality cheeses, all in a variety of formats, recently faced a packaging dilemma due to an underperforming machine.
The company is proud of its brand and sees its packaging as a natural extension, as such the shape form and function of its multiple packaging styles is tightly controlled. Indeed, in a recent packaging project Cama Group was asked to create an identical packaging style, but with more control over the final shape and the tightness of the sleeve around the product.
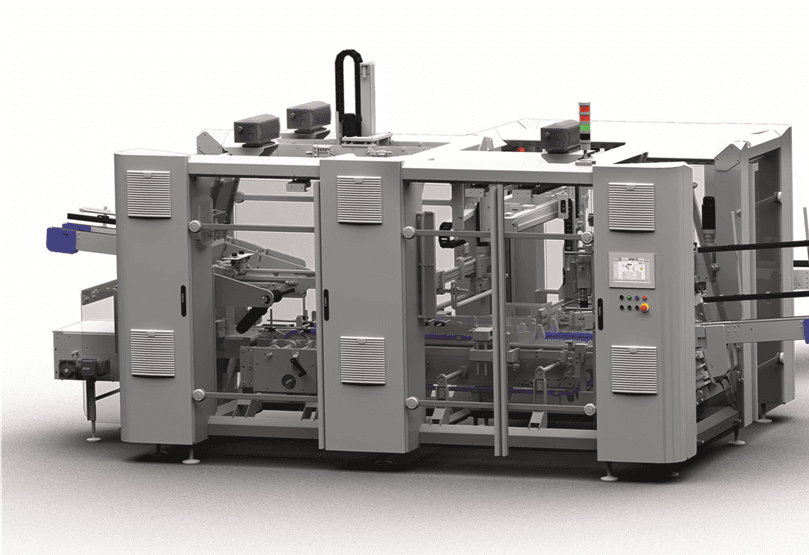
The product in this case was a two- section thermoformed tray containing a dairy-based snack. These trays were to be packaged vertically in 1 x 3 and 2 x 3 arrays, using a sleeve created from a cruciform-shaped blank.
The existing packaging system was simply not performing as expected, primarily due to the fact that the packaging style had changed and the incumbent machine, although capable of fulfilling its role, was neither efficient nor offered acceptable throughput. For this reason, the company approach Cama Group for a higher performing alternative.
“Our challenge was to develop an approach that could apply the sleeve, but not too tightly,” explains Davide Di Lorenzo, Sales Engineer Manager North America at Cama Group. “In order to achieve this – where tightness is normally preferred – we had to look at a completely different way of forming and combining the sleeve with the product. In effect, we had to build a solution and a complete machine around an existing sleeve blank.”
Cama Group’s solution took the form of a specially modified IF Series Top-Load Carton Sleeving System. Part of Cama’s Breakthrough Generation (BTG), the IF Series has design and operational features that are setting the standard in secondary packaging.
Their modular, scalable and hygienically designed frameworks house contemporary automation solutions – including advanced rotary and linear servo technology – which can be tightly coupled to in-house-developed robotics, to deliver the all-important flexibility and adaptability required by modern packaging operations.
The machine range is also based on a digital platform that supports full Industry 4.0 capabilities, including AR, VR and virtual testing, training and operation.
In operation, as opposed to being formed around the trays, in the new Cama machine the sleeve is formed without glue or the product being present. The products are then collated and oriented into pockets on a racetrack conveyor.

Groups of three are then picked up by a robot, rotated and loaded into the pre-formed sleeves. Glue is then applied to the lateral flaps which are closed and then the top flap, which is secured by the sleeve being inverted and pressed. Using this approach equal pressure is only applied at the end and the package maintains its more-uniform right-angled corners.
Robots are used extensively in the machine for their speed, repetition, accuracy and flexibility. One robot is used for sleeve erection, a second for product loading, a third for the first flap close and a fourth for the final flap close. When the packaging array is changed the robots can be instantaneously reprogrammed for the new format.
“It sounds relatively straightforward,” Di Lorenzo explains. “But this was actually a very tough project as we had to approach a fairly ordinary packaging application from a very different direction. In many projects we offer the services of our packaging-design team, but in this instance, the packaging design was not the issue, it was the packaging process.”

The project also involved the design and delivery of a case packer, which took the packaged snacks from the IF Series machine. “This was just as interesting as the sleeving solution,” Davide tells us. “As we were able to call upon our packaging design team in this instance, which was able to enhance the dimension of the case, not only saving materials and but also optimizing the eventual pallet-loading configuration.”
The existing solution used an American RSC case. Cama’s design team developed a flat-blank-based solution, which was not only smaller – saving 43% of materials vs the RSC design, but also resulted in an extra row of four in each pelleted layer – from 4 x 4 to 5 x 4. The new case design also reduced carton stock holding.
“We were also involved right from the beginning – at the system engineering stage,” Davide concludes, “so we were able to give our customer all of the benefits of our digital design, development, test and commission approach. This digital approach also spills into machine operation, changeover, maintenance and reconfiguration, giving the customer the best possible agility to cater for changing market demands. Digitally based flexibility and agility are essential in today’s market, but when they are supported by knowledge, domain experience and empathy, it becomes a much more powerful package.”