ENOBERG high-tech solutions
Beverage and liquid food industry has constantly been evolving to meet the several requirements of a market that keeps changing and that pays increasing attention to environmental issues.
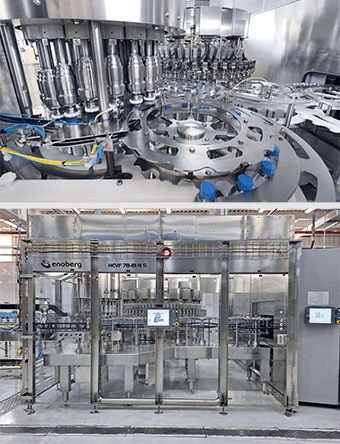
The filling machines used for the beverage bottling adopt more and more sophisticated technologies to fill different types of containers, mainly glass and/or PET bottles in the fastest and most precise way, thus ensuring company competitiveness and improving production efficiency.
Present on the market since 1984, ENOBERG (company of the SMI Group) is one of the main producers of filling machines for still and carbonated beverages in the world.
Reliability, solidity, ease of use and wide customization possibilities are features that distinguish the fillers supplied by ENOBERG.
Filling
Why is it important?
Filling is the most important stage of the bottling process, since quality, hygiene and preservation of the product characteristics depend on this operation.
Suitable for the filling of PET, glass and aluminum containers, ENOBERG solutions perfectly adapt to the filling of still (water, isotonic drinks, juices, sauces, vinegar, spirits, oil) and carbonated beverages (water, soft drinks, beer).

The response of ENOBERG
HYPERCLEAN range
To meet the requirements of hygiene, safety and cleaning and to minimize the possibility of contamination of the product to be filled, ENOBERG has developed the HYPERCLEAN series that offers considerable advantages in terms of hygiene, reliability and maintenance.
One series
Many advantages
The advantages in terms of hygiene
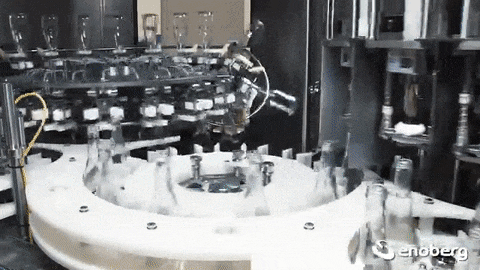
- the structural parts of the machine are designed in order to avoid liquid stagnation
- the inclined base plane ensures the continuous drainage of the liquids from the filling environment to the outside
- the welded frame is made of AISI 304 stainless steel, without iron components, which ensures a solid structure, with no rust
- the filling section is completely isolated from transmissions, that do not enter into contact with the liquid to be bottled
- the filling valves are made of AISI 316 stainless steel
The advantages in terms of reliability
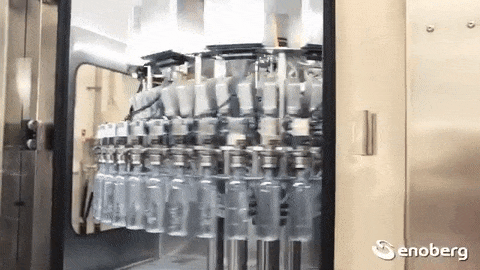
- fillers designed according to Industry 4.0 parameters
- complete process automation and electronic management of the movements
- the machine carousel movement is performed by robust gears positioned within the machine base
- fast format changeover of the bottle guide equipment
- parameters of each format manageable directly through HMI
The advantages in terms of maintenance

- compact structure allows to optimize the spaces of the production plant
- compact and easy-to-manage solution
- extremely safe access to the different components of the machine by the operator
- reduction in maintenance times and costs
To have further information on ENOBERG product range, do not hesitate to contact us.
