Turnkey solutions for machinery, spare parts, and technical assistance in the water and beverage industry
BBM Service is an Italian company with a long and renowned experience in the beverage sector, internationally recognized for the quality of its services. Specializing in the turnkey supply of bottling plants for water and alcoholic and non-alcoholic beverages, BBM stands out for its flexibility, speed, and ability to work on all types of machinery in the production line, supporting clients through every phase of the production process.
A TRUSTED PARTNER FOR MAJOR BEVERAGE BRANDS
For 20 years, BBM Service has collaborated with some of the leading brands in the industry, such as Nestlé Waters, Coca Cola HBC, Refresco Group, Heineken, and many others. This strong network of partnerships demonstrates the trust placed in the company and its ability to respond with efficiency and professionalism to the needs of major market players.
BBM’s strength lies in its ability to act as the single point of contact for clients, managing every phase of the process, from market and budget analysis to final delivery and commissioning of the plants. Thanks to a comprehensive and integrated approach, BBM Service offers turnkey solutions that cover the entire production cycle, ensuring optimal results in a short time.


BBM SERVICE’S KEY OFFERINGS
1. Used bottling machinery: excellence in sustainability
BBM Service is a leading player in the market for used bottling and packaging machinery. The company boasts an inventory of over 200 used machines, fully overhauled and updated, ranging from blow molders to fillers, from labelers to shrink wrappers, and even palletizers and wraparound case packers. Each machine undergoes rigorous quality testing to ensure optimal performance and long life.
One of BBM’s major strengths is the speed of delivery: with a readily available stock, the machines can be customized and installed at the client’s site within just 120- 150 days. This approach minimizes downtime and ensures essential production continuity for clients.

Choosing to purchase used and refurbished machinery not only represents a cost-effective solution but also a sustainable one. In an era where industrial waste management is an increasing challenge, BBM Service promotes a green approach, recovering and renewing machinery that would otherwise be discarded. This sustainable philosophy aligns with the commitment of many companies in the industry to reduce their environmental impact, offering solutions that respect the environment without compromising on quality.
BBM now offers three distinct purchasing options, tailored to different operational needs:
• AS-IS:
This option is ideal for customers seeking immediate availability and a highly cost-effective investment. By purchasing machinery in its current condition, clients can quickly start or enhance a production line with minimal delay.
• OVERHAULED AND GUARANTEED:
For clients who prioritize long-term reliability, BBM offers fully overhauled machinery, complete with a six-month warranty. This option ensures peace of mind, with the assurance that all equipment has been rigorously tested and refurbished to meet the highest standards of performance and safety.
• READY-TO-USE:
This comprehensive package includes operational machinery and a compatible spare parts kit, allowing for self-service maintenance. It is an ideal solution for businesses with an in-house maintenance team, providing everything needed for smooth and efficient production.

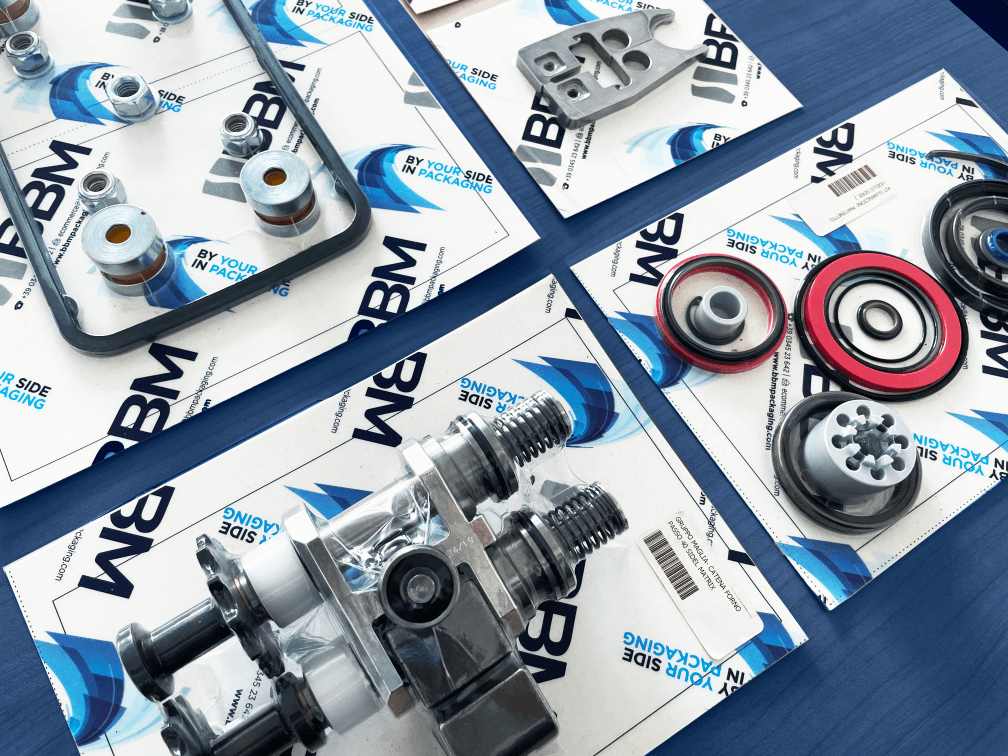
2. Spare parts: a reliable and cost-effective solution
BBM Service also excels in providing mechanical, pneumatic, and electronic spare parts compatible with the leading brands in the industry. With a warehouse spanning over 1,800 square meters, the company ensures wide parts availability, minimizing waiting times and ensuring quick delivery.
The spare parts supplied by BBM are tested in a certified laboratory, guaranteeing quality and reliability at competitive prices, 10-20% lower than the market average. For regular clients, BBM offers dedicated discounts and the possibility of creating a customized stock of essential spare parts for routine maintenance, ensuring more efficient warehouse management and significant cost savings.

An innovative aspect of the spare parts service is the ability to mark the parts, facilitating identification and ensuring traceability. This system allows for precise control over the components used, enhancing safety and efficiency in the production process.
Discover the full catalog of compatible spare parts.
BBM has also developed a minimum stock program that ensures the availability of essential spare parts, allowing clients to maintain uninterrupted production. Furthermore, in the first months of 2025, BBM will launch a new e-commerce platform dedicated to selling compatible spare parts, further simplifying the purchasing process and reducing management times.
3. Technical assistance and engineering: complete customer support
With over 20 years of experience and a team of more than 50 qualified technicians, BBM Service offers a wide range of technical assistance services to support clients. These include disassembling and relocating production lines, format changeovers, scheduled maintenance of plants, and staff training. The company also provides remote assistance through a HOTLINE service, offering personalized packages to respond quickly to client needs and ensure a rapid production restart.
BBM Service also stands out for its expertise in highly specialized engineering interventions. BBM’s portfolio includes machinery upgrades aimed at improving energy efficiency and reducing operating costs. BBM is a leader in upgrading blow molders, achieving energy consumption reductions of up to 35% through targeted and customized installations.
The turnkey approach and the ability to provide complete service, from initial consulting to plant commissioning, make BBM an ideal partner for beverage companies looking to improve their production efficiency and reduce operating costs.
