Multiple contemporary studies support the fact that companies that have exploited the digital capabilities of their assets – either as part of a transformation, or a general move to a more data-capable infrastructure – are weathering the effects of the COVID-19 pandemic more effectively… and more robustly.
Although many of the technologies being exploited by these companies are perceived as being fruits of “the new normal”, many actually find their roots in more established practises, which are finally getting the airplay they deserve – albeit as a short-term necessity as opposed to being part of a long-term technological plan.
Many of us have taken part in some form of virtual meeting, with and without video, and are used to dealing with project-team software, which adds a further level of distanced inclusion. But arguably, from an engineering sense, one of the most powerful tools at our disposal is augmented reality (AR).
By giving engineers and operators an immersive, intimate and highly interactive appreciation of a machine – sometimes before it has even been built – augmented reality could very well be the foundation of Industry 4.1 – thanks to its ability to deliver incredible levels of information & presentation… based on the data delivered by Industry 4.0.
From an end user’s perspective, the good news is that AR does not rely on an installed digitally transformed base of operations. Using CAD data, OEM suppliers can deliver this immersive technology far more easily than many think.
“As a leading secondary packaging machine supplier to all of the major global vertical markets,” Massimo Monguzzi R&D Manager, at Cama Group explains, “it is a pre-requisite that we must exploit and deliver the very latest features that technology can provide.
Augmented reality has always been part of our roadmap, as has virtual commissioning and testing, but the global pandemic has pushed the need for these technologies right to the forefront.
“From our perspective, having a digitally capable platform already in place– in the form of our BTG range of machines – has made the transition for us and our customers a lot simpler,” Massimo Monguzzi R&D Manager continues. “Like many companies, we have the in-depth CAD data that forms the foundation for our AR offering, but unlike some others, our exploitation of fully interconnected digitally capable hardware and software means that our AR solutions can be used for full simulation, as opposed to just creating pretty 3D images to show a customer.
“A case in point would be for a recent application we developed for a well-known household brand. Augmented Reality very quickly made it onto the customer’s wish list following the travel and distancing issues presented by the pandemic,” Massimo Monguzzi R&D Manager-explains. “The COVID-19 situation led to global difficulties in location based training and, as this was a brand-new machine for the customer, it asked us to look at how we could help speed up line operation by helping it get to know how to use the machine more quickly. The customer recognised that AR was ideal for training – even before receiving the machine – and wanted to start experimenting with the technology in order to get more confdent in oSerations and procedures.
“We were able to deliver a virtual version of the customer’s precise machine thanks to highly detailed CAD data,” Massimo Monguzzi R&D Manager adds. “Using this platform there were no surprises when the machine was delivered – there was nothing new… the operators already knew it intimately from the AR/VR models.
“This may sound like a relatively simple and obvious deployment of the technology, but AR offers so much more potential throughout a machine’s entire lifecycle,” Massimo Monguzzi R&D Manager elaborates. “It has the capability to deliver value at all the primary stage gates: tender, design, testing, installation, commissioning, operation, changeover, maintenance, support and modifcation ,Indeed, there are very few operational facets of a machine where AR cannot play role and add value.”
From the outset, at the design and prototyping stage, customers can get a clearer appreciation of the machine and fully understand its capabilities. Operation can also be fine tuned thanks to simulations based on accurate product models – and this is before any metal has even been cut. At this stage, the machine can be virtually superimposed into its proposed location, too, and then manipulated, so any utility and real-estate issues can be solved prior to install.
Installation, commissioning and FAT are also helped with representative models and those undertaking the testing can be given informative and unambiguous instructions, all of which can be logged and recorded as part of the procedure. In addition to the aforementioned familiarisation, AR has more to offer in the operational phase of a machine’s life.
As well as training new operators,
it can be used to deliver over-layed instructions and videos for component changeovers and batch-change procedures. This visual on-machine feature is also exploitable for maintenance operations and for the addition of revised hardware and sub-systems.
“Our deployment of contemporary automation solutions means that these Industry 4.0 capabilities are in easier reach for customers,” Massimo Monguzzi R&D Manager-explains, “even for those with older machines, as the AR capabilities feed off the original 3D CAD data, which lives on our design servers. We have seen incredibly positive real-life results recently, where they
have proved vital for FATs, training, maintenance and operation, all delivered and performed virtually!”
“We are boxing up AR and other digitally enabled capabilities into what we call 4.0 Packages,” Massimo Monguzzi R&D Manager adds.
“These can comprise a combination of technologies, which can be tailored and adapted to the needs of the customer and application, and can cover anything from day-to-day operation, through consumable consumption and on to energy efficiency We are also heavily involved in the development of auto changeover solutions with the absolute minimum need for human interaction. The idea being that the machine will prep itself for changeover using servo technology and the operators will only be involved where changes cannot be done automatically.
“Compared to the market average,” he adds, “we offer quicker changeovers than most, but the market is demanding even more.
Today we have managed to cut changeover in half – from 30 minutes to just 15. In coffee production, for example, where production
speeds and outputs are so high, saving even 15 minutes per changeover is vital.
If there are 10 production changes per day, which is not uncommon, this equates to 2.5 hours of additional up time! Payback for the additional technology is less than one month!”
AR has always been on the future road map, but has rapidly evolved from a cool feature that companies imagine using one day, into a must have technology that everyone needs to use every day. When the world returns to normal, AR will be one of the tools that stays in regular use… everywhere.
It is too good to use merely as a stop gap. It adds value, saves money, solves problems and makes everyone’s life so much easier, what’s not to like.
And the best thing is, you don’t need advanced hardware to make it happen, just companies with their fingers on the technology and market pulse… such as Cama.
www.camagroup.com
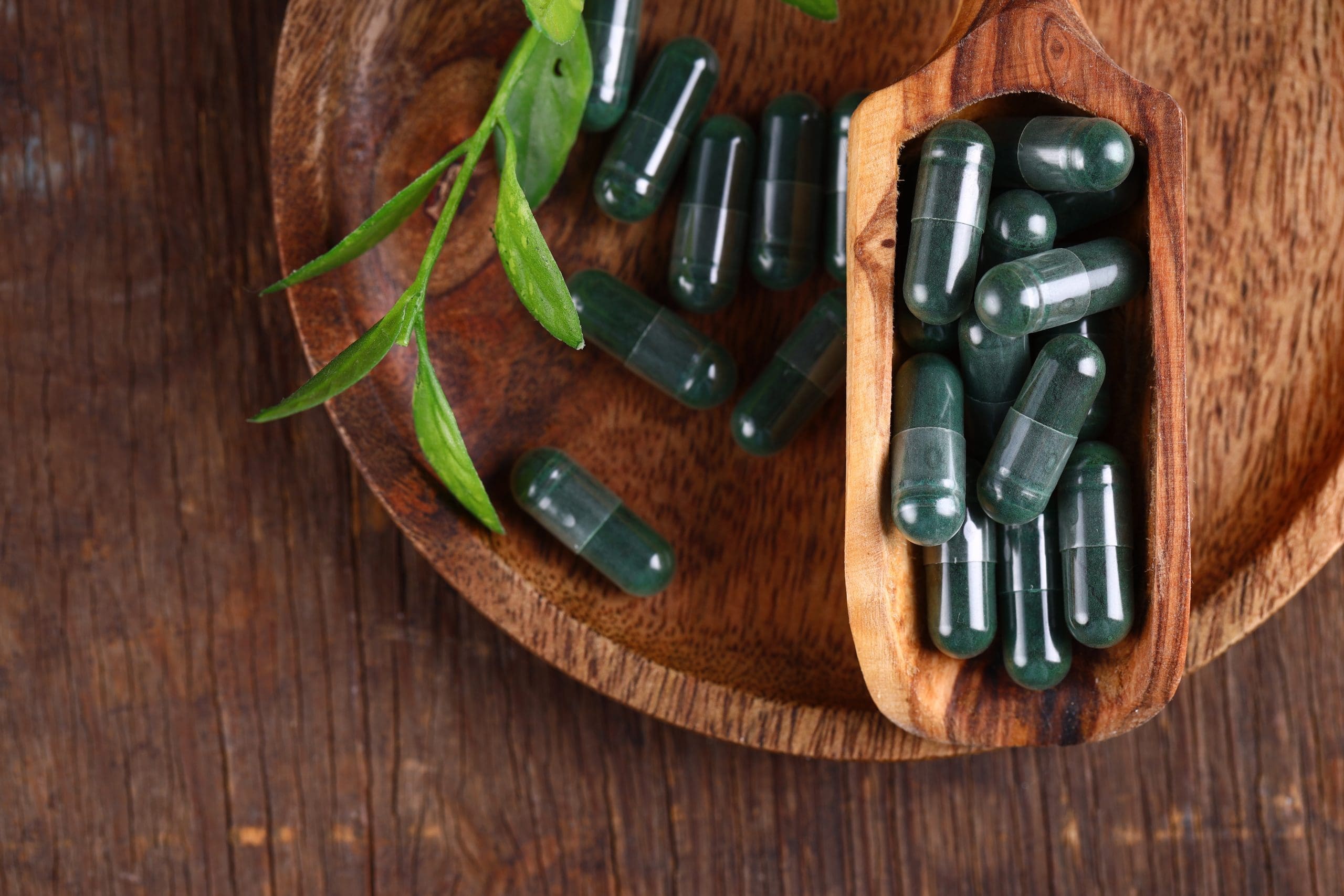
Controllo della quantità di riempimento ad alta precisione nella produzione di integratori alimentari
Sulla bilancia, pronti, qualità! La selezionatrice ponderale Flexus® e la soluzione software