The performance of end-of-line packaging systems plays a key role in ensuring an efficient production, capable of quickly adapting to market changes and improving the quality and sustainability of the final packaging of beverages, food, detergents and chemical products. SMI automatic palletizing systems from the APS ERGON range represent the ideal solution for managing an uninterrupted, optimized and flexible production flow, capable of quickly switching from one format to another, according to the consumers’ purchasing habits.
An example of this flexible technology is represented by the APS 4140 L ERGON palletizer, which stands out for the perfect synchronization between pallet loading, palletizing layer formation and interlayer insertion.
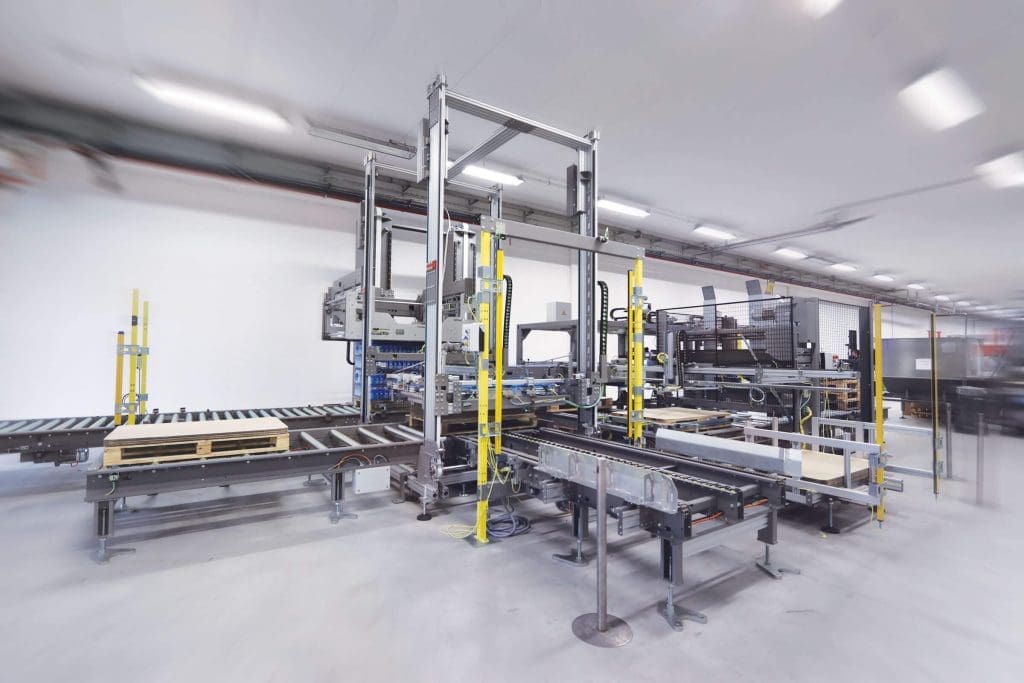
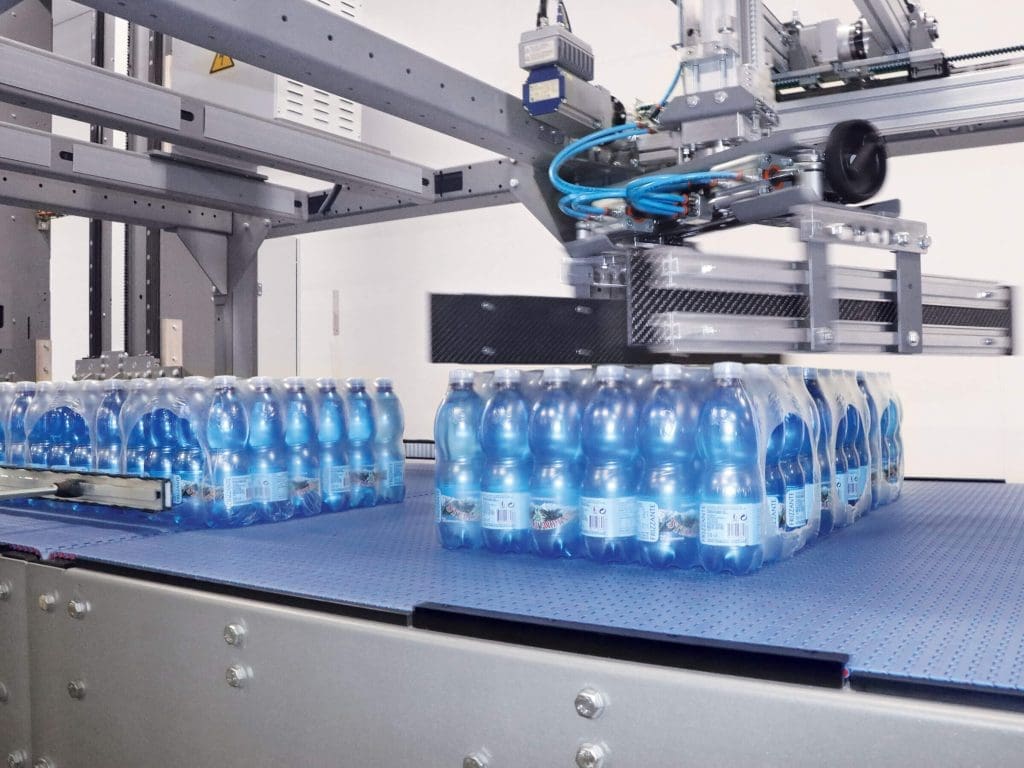
More efficient end of line with double column palletiser
The APS 4140 L ERGON system is an advanced system equipped with two independent columns for palletising cartons, bundles, trays and packs in general up to 140 packs per minute/400 layers per hour (variable values depending on the product) It consists of several modules that can be configured individually according to the logistical conditions of the end-of-line area and palletising needs.
The heart of the APS ERGON system consists of the two vertical columns: the first equipped with a motorised belt, while the second with a basket.
Through an innovative system of rotation and/or continuous pack handling on three Cartesian axes (x, y, z), the bundles arriving on the single-row belt are turned, translated and arranged in several rows in the position provided by the palletising pattern, thus preforming the layer.
The first column receives the complete layer from the input module and, moving on the vertical axis, brings the product to the height of the basket of the second column; From here, through the motorised belt, the layer is inserted into the basket that deposits it on the pallet.
At the end of this operation, the basket, moving on the vertical axis, moves to the waiting position of the next layer.
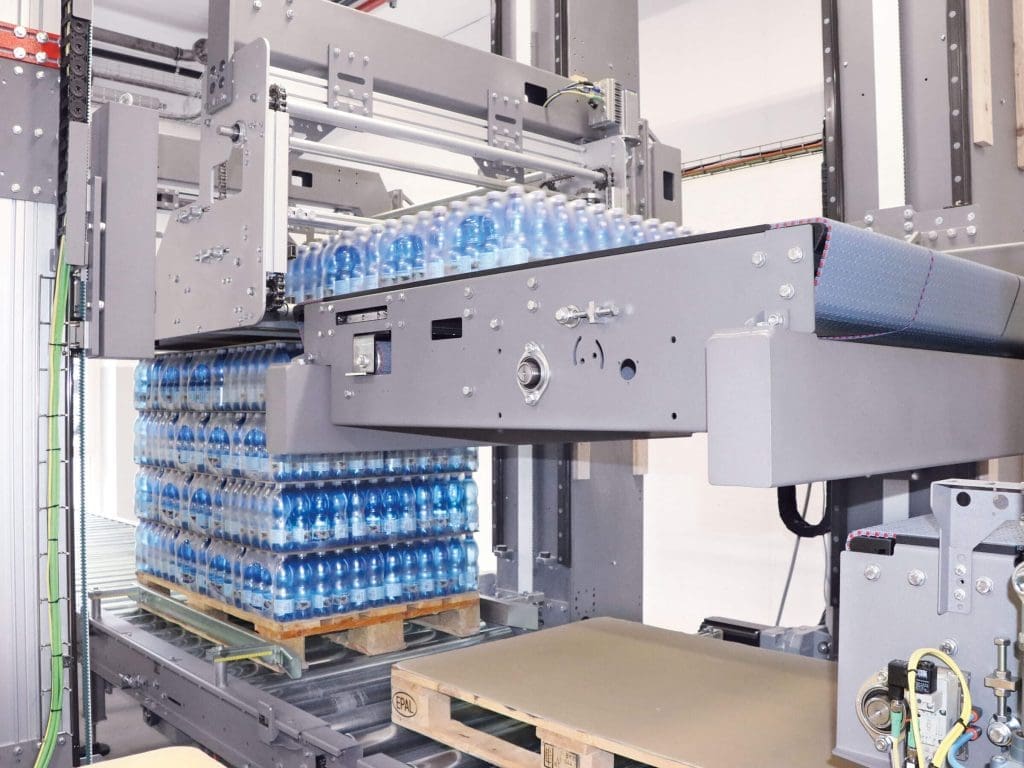
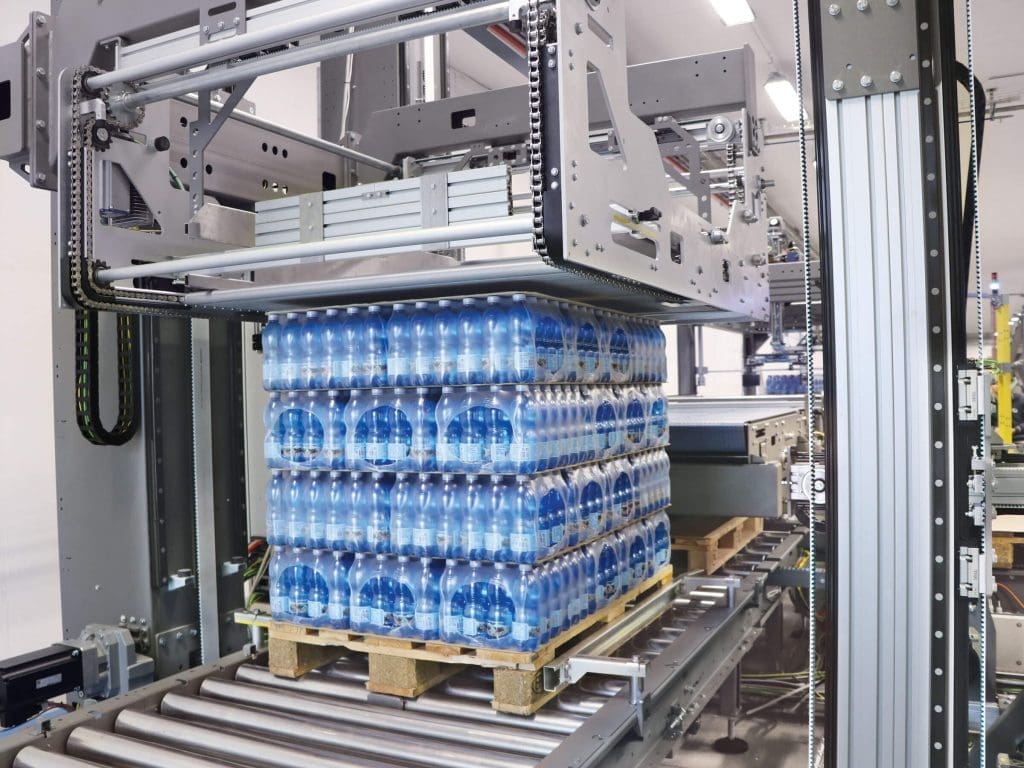
Advantages
• The inlet with continuous preformation is very compact and allows the end of line spaces to be optimised.
• The layer formation system is equipped with rounded, sliding protection doors in anodised aluminum, which allow all the motors (low energy consumption) to be on the outside of the mechanical groups they operate.
• The door closure system is equipped with a deceleration device, which slows down the final phase of the cycle by accompanying the door harmoniously.
• The ergonomic and functional structure of the frame allows the operator to easily carry out all the activities related to the use and maintenance of the system.
• The accident prevention protections are made of aluminum and polished polycarbonate (PC).
• Production adapts quickly to new formats required by the market.
• Palletising schemes are optimised for truck loading.
• Format changeover times are kept to a minimum.
• The handling of the containers is fluid and avoids damage during handling.
• Use of innovative design solutions in IoT key, which reduce the operator’s workload and ensure high levels of plant efficiency.
• Simple and intuitive control of all operations, which can be further optimised with the SWM supervision system for the collection, control and interpretation of production data.
• ICOS motors equipped with integrated digital servo-drive, which ensure production with reduced environmental impact and low energy consumption.
Pallet feeding system
Magazine module with a maximum storage capacity of 300 kg (pallet modules with higher capacity are available as optional accessories) and/or a maximum total height of 1800 mm.
The system is designed according to FCR (Full Cost Reduction) methodologies and is tested and supplied to the customer full wiring and assembly.
Optional pad feeding module
It is a module composed of the pad magazine and the pad feeding unit with controlled axes, which can be combined with the central column of the APS ERGON palletiser.
The pad feeding module is a pad feeding system that can be adjusted according to the different dimensions of the interlayer.
SMI S.p.A.
SMI supplies a wide range of bottling and packaging machines with an innovative design, equipped with IoT technology, that offer smart solutions for productions up to 50,000 bottles/hour and that meet requirements of competitiveness, efficiency, flexibility, energy saving and easy management of the production plant.
