We live in years in which the dominant theme, both in mass communication and in industry, is sustainability. For many, this term immediately and solely recalls that of environmental sustainability and the impression is that we tend to neglect other equally important aspects, not least the economic one.
Even in the world of packaging we can see this phenomenon, with the right push in the direction of packaging that uses less plastic or is made of innovative, compostable materials. There is, however, another issue, until now perhaps taken a little for granted, which is once again gaining importance: production efficiency and waste reduction.
Packaging lines are a complex organism, composed of numerous machines in series or in parallel, and no matter how well constructed and efficient the newer ones may be, the overall efficiency will inevitably drop.
Conveyors are the circulatory system of this organism and the inclusion of a buffer or accumulation system between them is crucial to recovering lost efficiency.
These systems handle operational discrepancies or short stops, keeping production running smoothly. For example, a machine working intermittently can cause problems when connected to one that requires a constant flow, but while this can often be solved with a few extra metres of ‘parking’ belt, handling micro-stops requires a belt system that becomes a real machine.
The BAT-Buffer from M.H. Material Handling is a flexible accumulation system with a configurable structure in anodised aluminium or AISI 304, adaptable to many different products.
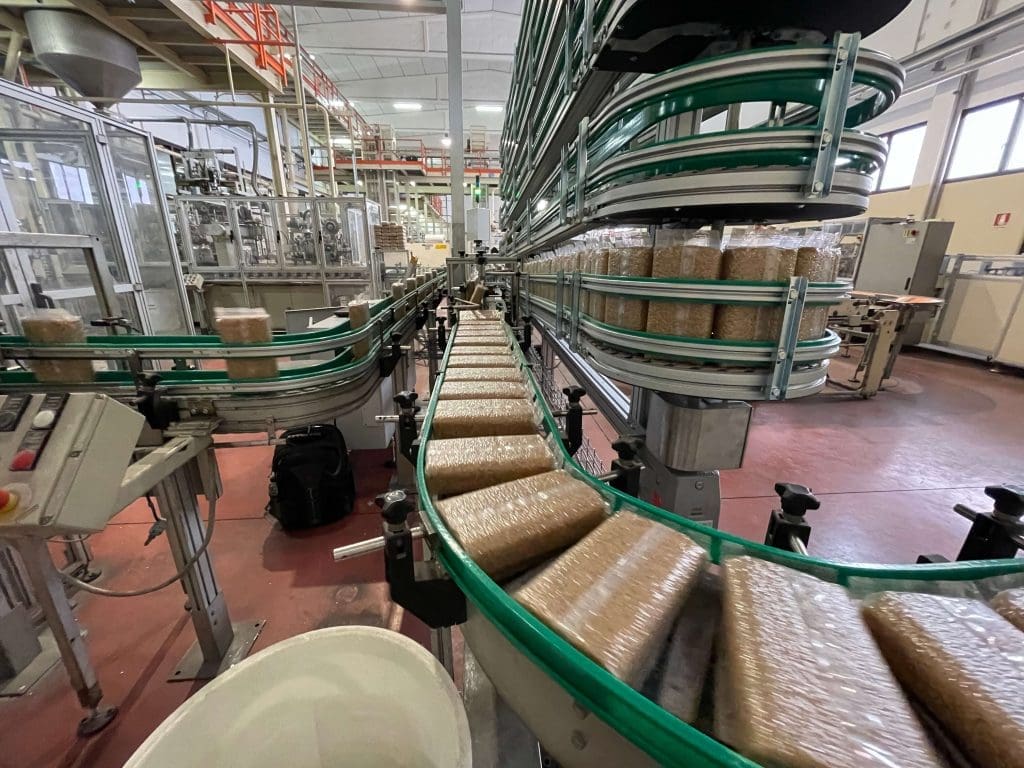
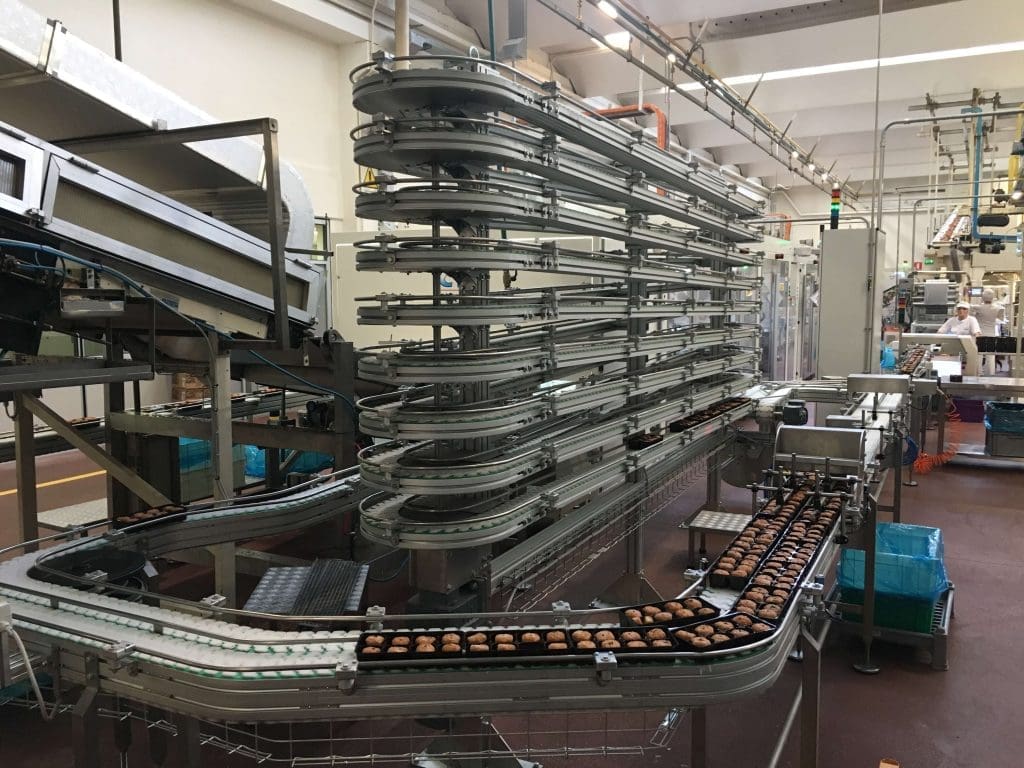
This spiral device offers up to 150 metres of accumulation space with only one motor. The structure of the machine is made up of spirals with straight sections varying between 2.5 and 6 metres in length and curves with an average radius of 200 mm to minimise side encumbrances.
The system operates with LIFO logic, when the machines downstream stop the products are extracted from the line via a diverter that sends the products to the buffer.
The movement of the chain is controlled thanks to the action of an inverter and a inlet flow photocell; this allows the insertion of the products on the buffer by controlling the pitch so that they do not come into contact with each other, maintaining zero pressure and avoiding possible damage, while maximizing the available space.
When the downstream machine becomes available again or in the event that upstream production stops, the buffer reverses its direction of travel and begins the unloading phase thorough a merger system that allows to mix what comes from the spiral with the normal production flow and, if the downstream machines have 10-20% extra capacity, allows the elimination of losses at the end of the shift.
Ideal for baked goods, confectionery, coffee and others, it will be on display at FachPack 2024, Hall 7, Stand 757.
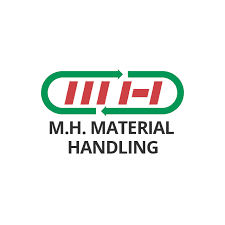