Despite the name, WATER SYSTEMS is not only involved in water purification systems but is specialised in the production of complete solutions and plant designs for medium-large CSDs and juices projects as well.
All the steps involved in the production of mineral water, soft drinks and juices – from water purification, right through to syrup preparation, blending, carbonating, mixing and pasteurising and eventually including utilities supply as well for a real turnkey solution – are available from a single supplier at WATER SYSTEMS: this is clearly an important advantage allowing the bottler to save time during processing equipment design, project execution and equipment maintenance.
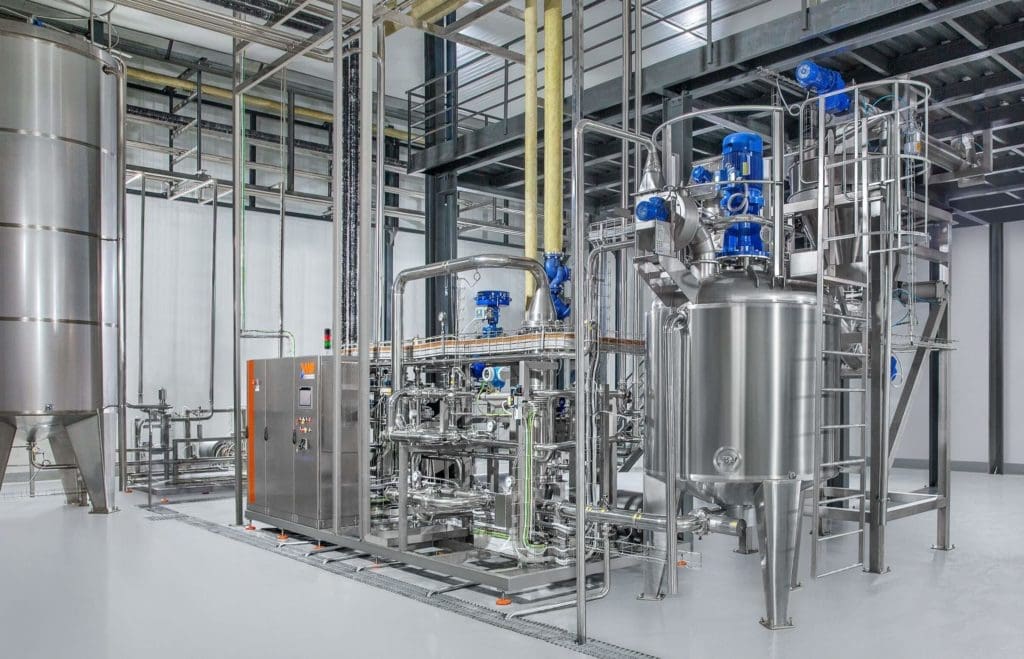

WATER SYSTEMS recently installed and commissioned a new turnkey solution on a greenfield project in Nigeria with one of its historical partners in the beverage business: aimed to maximize sustainability thus minimizing energy consumption and water wastage, the entire scope of supply has been oriented to fulfil these goals; by the way the syrup room – probably the most automated unit present in an African beverages factory up to now, featuring more than 120 mix proof valves and conceived to maximise the efficiency of equipment regardless of the number or level of specialisation of operators – is the most representative part of this plant.

The market of beverages is very wide due to the growing diversification in terms of quality and variety of drinks (both alcoholic and non) required by Consumers. Therefore, the producers, to answer quickly, need to process a wide range of ingredients (powder as well as liquid).
In some cases, such ingredients might require a special treatment according to their features (texture, reaction, viscosity, solubility, temperature-sensitivity, flammability and so on). The innovative design of the WATER SYSTEMS’ syrup room ensures automatic ingredients and CIP fluids loading as well as the automatic outlet through clusters of mixproof, single seat and butterfly valves dedicated to syrup tanks and ingredients preparators and sources.
Syrup rooms provided by WATER SYSTEMS’ are designed on stand ard modules which are customised for each specific project according to specific needs. Furthermore, the equipment always features a noncompromising technology for what concerns cleanability and hygienic aspects: CIP fluid paths are covering any part of the plant – including process water distribution lines – and the entire piping is tooled to avoid dead legs and minimize the number of weldings. In-house preassembled modules configuration allows plug and play quick installation granting Customers an immediately available system.
State-of-the-art technology for liquid mixing ensures that the sugar syrup, the flavours and all the required ingredients are optimally mixed and distributed to grant a perfectly homogeneous concentrated product and the best deaeration process; this benefits
Customers in three different ways:
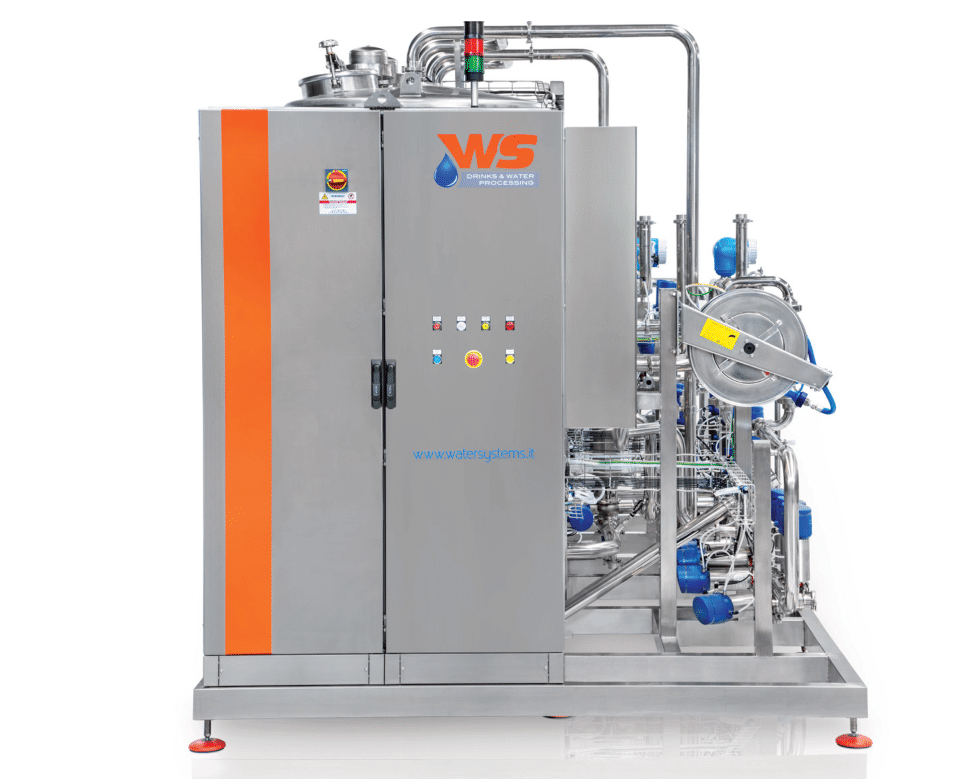
– shorter mixing and deaerating time corresponding to quicker production cycles;
– optimal low-shear mixing of low and high-viscosity fluids to prevent oxygen pickup and fruit’s cells damaging in case of pulpy ingredients;
– lower energy costs through unique energy-saving impellers’ design.
WATER SYSTEMS’ syrup rooms can be flexibly extended thanks to modularly arranged skids: the design always take into consideration future Customer’s expansion plans and the maximum allowed number of bottling lines that can be fed is four; the syrup output flow rate can be individually adjusted to suit each bottling line need.
All instruments and regulation systems dedicated to the control of individual syrup and product components are characterised by the highest precision in the processing in order to grant an accurate ingredients blending and to minimize product wasting during circuits emptying.
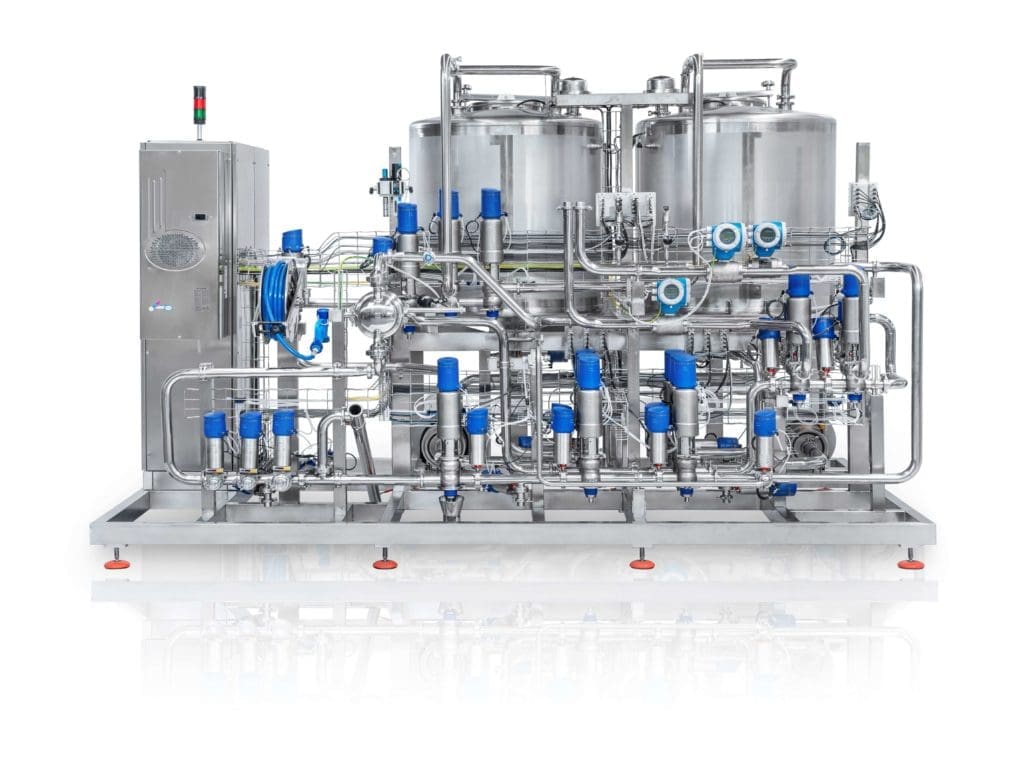
Using the new pulse and burst technology for valves cleaning, trials have revealed that up to 90% of CIP liquid can be saved – significantly lowering the operating costs compared to the traditional (PLC) timer-controlled seat lift; further information are available at: https://food.alfalaval.com/thinktop-rethought-burstseat-clean
WATER SYSTEMS’ syrup rooms are conceived to ensure and safeguard the perfect ingredients blending and always aim to meet the needs of all the Customers who are looking for high quality product.
For more information and to discover the range of products visit the site.
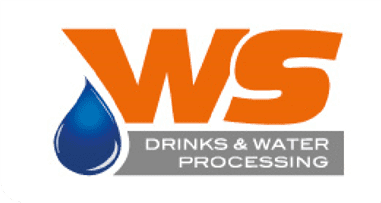