In recent years there has been a strong growth in the market of gallon water bottles, both in Italy and worldwide. Dispensers showed a positive trend, apart from the temporary setback caused by the Covid-19, mainly involving offices, factories, warehouses and various communities.
The success of gallon bottles, in particular those of reusable PET or PC bottles, obviously involves the need to guarantee the safety of water, and consequently the cleaning of containers and dispensers. Which must be accurately and periodically sanitized.
The water used to fill the gallon bottles, which can be natural spring water or water from other sources, must comply with the quality parameters defined in Community legislation on water intended for human consumption. Used empty gallon bottles, if still intact, can be reused. But before being inserted in a new filling cycle, they must be inspected for integrity, absence of discoloration and possible odours.
After that, they must be washed with water and specific detergents and rinsed thoroughly with special machines. Like those built by Akomag, for example, an Italian company specialized in the design and production of machines and plants for the bottling industry.
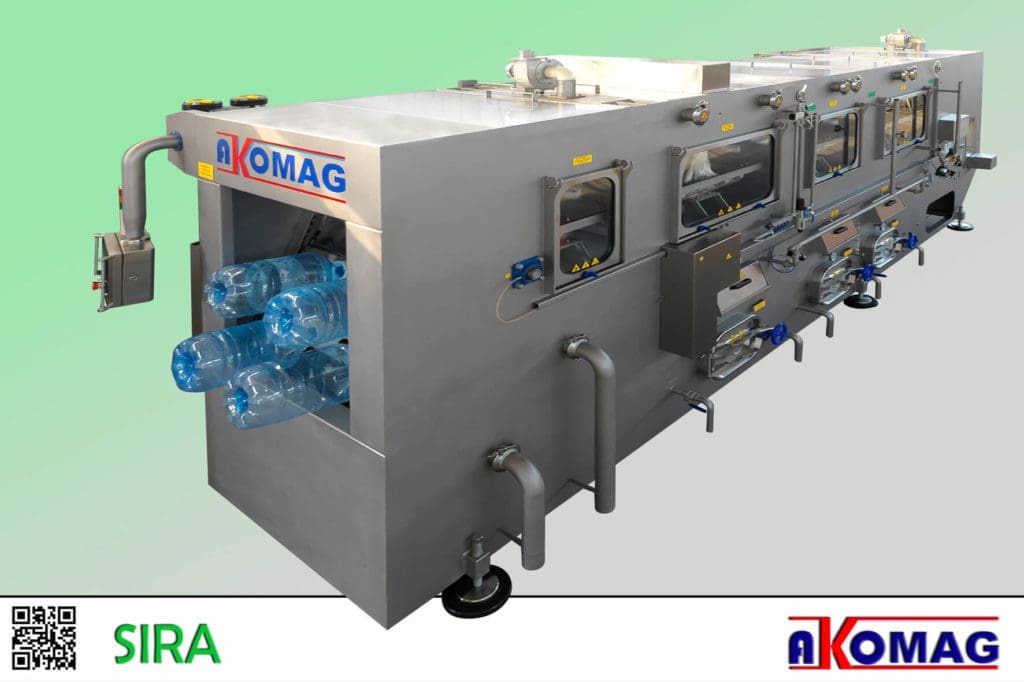

Washing, rinsing, filling, capping
The Monobloc washer for gallon bottles Sira has been designed by Akomag for washing and sterilizing PET or PC gallon bottles or other bottles of various sizes, to be filled with still water.
The washing cycle adapts to the various production needs of the end customer and is very effective. For this machine Akomag has designed and produced a special spraying and brushing device for gallon bottles that ensures total cleanliness.
Through the use of special mobile nozzles furniture (penetrating and rotating), the machine washes the bottle internally at high pressure (5 bar). While the outside is brushed by means of nylon brushes. The machine can be quickly adapted to the different bottle formats by simply setting the type of container to be handled on the control keyboard.
The stainless steel control board installed next to the monobloc is easily accessible for the operator. The panel is equipped with a touch screen for the complete management of all line functions, and the display of operating parameters and alarms.
The Monobloc features an automatic de-capper in stainless steel: a pneumatic system grips the bottle neck while ejecting the cap.
The system is safe, but it can be equipped with a system for the selection and ejection of gallon bottles that have not been properly de-capped.
The bottles are then filled by means of special inverter- controlled pumps. A valve designed by Akomag guarantees a laminar flow and no contact between the valve and the bottle.
The filling is carried out by means of a special metering device that ensures extreme filling accuracy. The capper consists of soundproof vibrating hopper, a descent channel, and a tear-off pick-up head.
The closure of the bottle is guaranteed by an inclined pressure belt characterized with adjustable pressure. All adjustments are automatic and managed from the control panel.
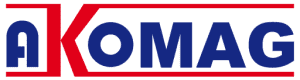