Livetech selected Rockwell Automation solutions to build a secondary packaging line for Galbusera-Tre Marie, an Italian brand with a long history in the bakery industry and with a strong commitment to preserving the craft-made quality of its cakes.
Background
For Galbusera, an Italian company formed in 1938 in Morbegno, in Valtellina, the quality of its baked products – biscuits, snacks and crackers – has always been a priority. In 2014 Galbusera acquired Tre Marie, a Milan-based brand with a long tradition in the production of Italian panettoni and colombe and launched an important investment plan to modernize its manufacturing lines.
Since January 2018, Tre Marie leavened products – colombe and panettoni – have been produced in the new plant in Vellezzo Bellini. Tre Marie products have always been characterized by their craft made taste, which is the result of a long and delicate production process: “Seventy-two hours are needed to produce a panettone or a colomba,” Franco Ronconi , Technical Director at Galbusera, explains. “Our technicians keep the craftsmanship of our products alive even if the process is highly automated: we bake and package 1,800 colombe per hour and 2,200-2,400 panettoni per hour.”
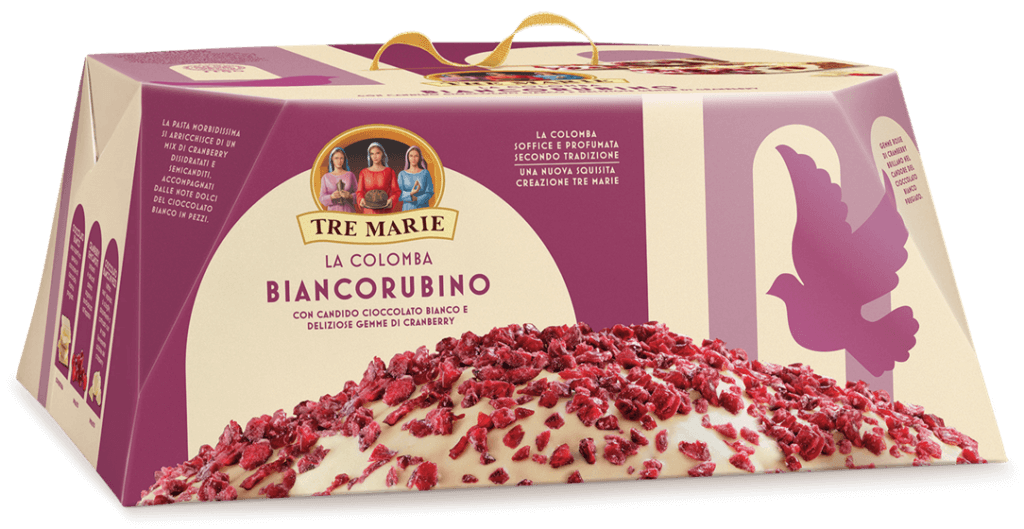

Challenge
When Galbusera transferred the production line from the Tre Marie headquarter in Milan to the new production site, a major renovation involved the leavened packaging process. “We were looking for a technology supplier that could give us a post-installation support too and we found out that Livetech could be the right one,” Ronconi says.
Livetech, a company delivering engineering, consultancy and production of complete packaging systems, proposed an innovative solution for the secondary packaging of panettoni and colombe; a system based on an automatic wrapping line that forms a display tray (couvette) from a cardboard die-cut. The line includes three robots that place the packed products on the tray.
As Federico Scornaienchi, Area Manager at Livetech, explains: “The display tray is a very smart solution for the employees in stores, as they don’t have to extract the products from any closed box to expose them; the so-called couvette is therefore a plus for Galbusera when contracting with deliverers and an interesting marketing tool, because the product is immediately visible and accessible to the end user as soon as the tray is placed in the store.”
Furthermore, in the secondary packaging process, the new solution offers several benefits compared to the American box, which was previously used by Galbusera. It is more flexible, because a cardboard die-cut can be used to form different tray models, while the American box has standardized dimensions; and it helps to save materials used for the secondary packaging, because additional background and cardboard internal dividers are not needed.
Galbusera decided then to transform its secondary packaging concept radically. The most challenging step of the project concerned the ability of the line to realize the right batches required by Galbusera sales office and to meet the palletizing requirements: “We had to respect the quantity per sale unit and per pallet,” Scornaienchi explains.
The manipulation of the finished product was another peculiarity that Livetech and Galbusera had to cater for: “We had to comply with severe constraints in moving the product along the secondary packaging and transporting steps.” Ronconi points out.
“Products can’t be allowed to deteriorate in their package, in terms of shape and appearance. Tre Marie panettoni and colombe are appreciated for their high quality and customers who choose them expect the same quality even in the packaging.”
Robots have to load the tray not only with carton-packed products, but also flow-packed products, which are conceived to be sold in outlets.
“In this second case, products in bags have to be picked and moved more delicately, because they are less protected than they are in a carton box, and we initially had some perplexities: could a robot deliver the same care as an operator’s hand?” Scornaienchi continues. “Thanks to special gripping tools and advanced control configuration, the robots are able to offer delicate handling, preserving the product in both cases.”
Solution
Livetech designed a multi-format line for Galbusera, in order to form, fill and close the trays. The first station comprises an automatic unit that loads and forms the die-cut cardboard. Three robotic islands are the core of the line: they take the products coming from the conveyor belt – which is connected to the primary packaging machine – and place them on the tray in the correct numbers. Different gripping tools are used depending on the package of the single product (case or bag).
When a format changeover is needed, the robots rotate towards the operator, who can replace the gripping equipment.
The tray then passes to a weighing station, where a cell verifies weight parameters: if they respond to set requirements – that is, the tray contains the right quantity of pieces – they move to the next robotic isle, where the robot puts glue to the edges of the cardboard die-cut and folds them, forming a containment perimeter.
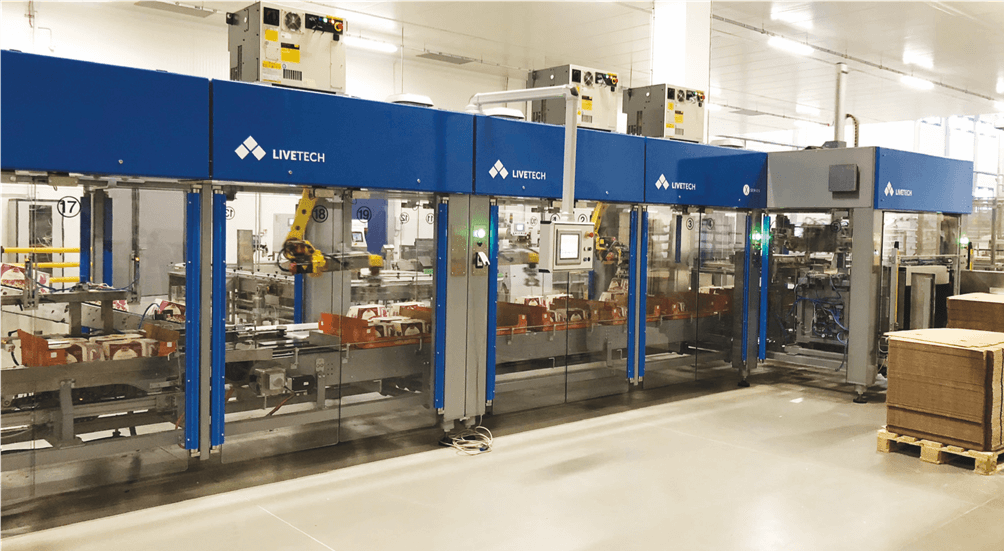
Then another piece of cardboard is placed above to cover the products. The trays are stacked one on top of the other, up to a maximum of three, and move to palletizing station.
The automation architecture implemented by Livetech is based on an Allen-Bradley® CompactLogix™ 1769-L36 programmable automation controller (PAC) from Rockwell Automation. This automation platform helped to minimize installation and startup time in Galbusera plant, thanks to a common software environment and an integrated axis control, which met the precision and speed requirements of the robotic islands.
Two Allen-Bradley Kinetix® 5500 servo-drives are connected to the controller, while four Allen-Bradley Kinetix single-cable VPL servo-motors are connected to the servo-drives. An Allen-Bradley PowerFlex® 525 variable-speed drive, an Allen-Bradley PanelView™ Plus7 graphic terminal and several Allen-Bradley POINT I/O™ modules complete the architecture.
The power system is a Rockwell Automation one too and is based on 1606 Series-XLS Switched-Mode Power Supplies. “Quality, integration and ease of use are the values we share with Rockwell Automation when it comes to selecting the right technology for a specific application,” Scornaienchi says. “The CompactLogix platform helped us to build a flexible multi-format line.”
Results
Thanks to Livetech and Rockwell Automation, Galbusera now has a more automatized secondary packaging process, without compromising the high quality for which its products are appreciated. Ronconi points out that in Galbusera automation is adopted where it’s worth: “The secondary packaging of small batches is still manual,” he says, “and our operators have the possibility to control and supervise the line.”
The Rockwell Automation platform helped to improve the flexibility of the secondary packaging line too: “We initially wanted to standardize the trays, but while developing the system, we changed our minds and chose a flexible solution, that had to be able to adapt the bottom of the tray according to the quantity of the pieces to be contained.”
The CompactLogix PAC with integrated motion allows operators to perform quicker format changeovers and doesn’t require the plant to be stopped upstream. Preserving and handling products correctly throughout the process is a must for Galbusera and thanks to Livetech and Rockwell Automation the Italian company got it: it can be sure that its colombe and panettoni come to the consumer in perfect conditions.
Challenge
Historic Italian bakery needed an upgrade path that balanced modern automation agility with delicate handling of its baked products.
Solutions
A Rockwell Automation solution was installed, which included:
Allen-Bradley CompactLogix programmable automation controller
Allen-Bradley Kinetix 5500 servo-drives
Allen-Bradley Kinetix single-cable VPL servo-motors
Allen-Bradley PowerFlex variable-speed drives
Allen-Bradley PanelView Plus7 graphic terminal
Allen-Bradley POINT I/O™ modules 1606 Series-XLS Switched Mode Power Supplies
Results
Common software environment Integrated axis control that meets the precision and speed requirements of the robotic islands PAC with integrated motion delivers quicker tray format changeover and doesn’t require the plant to be stopped upstream.