What can help a winery improve its process? How can costs be optimized in a winery? How can you work better and produce more without necessarily having to invest in buildings or water drainage systems? How can you do without compressed air? How can you be greener?
LAB-X and CAD-X, with their patented systems, completely revolutionize the work in the winery. The External washer/dryer with single combined carousel mod.
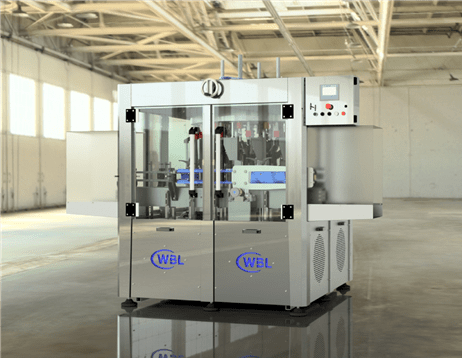
LAB-X opens the way to new washing concepts. It is the first machine in the world to enclose in a unique carousel the washing and drying phases, with a consequent drastic reduction of the occupied space.
1 – Most compact machine in the world
2 – Active surround system Automatic shape recognition brush system.
3 – Automatic brush wear compensation. The “tactile” washing device requires the brushes to advance towards the bottle up to the contact, recognizing the shape. Wear is compensated.
4 – Green washing system Water is dosed on the bottle in a smart way only where and when it is needed in a closed station.
5 – 3-Axes washing system improved cleaning efficiency.
6 – Totally self-lubricating No greasing points.
7 – Universal drying Innovative drying air distribution system.
8 – No compressed air on the whole range 9 – Water off system Injection system which recognizes the absence of the bottle and stops the dosage of water in the corresponding empty station
CAD-X radiant dynamic conditioner is synonymous with transformation and progress compared to traditional technology. It revolutionizes the bottle conditioning process.
It is a radiant conditioner with dynamic accumulation. Thanks to this device, water is totally eliminated in the process, consequently the system is perfectly cleaned and free from contaminations
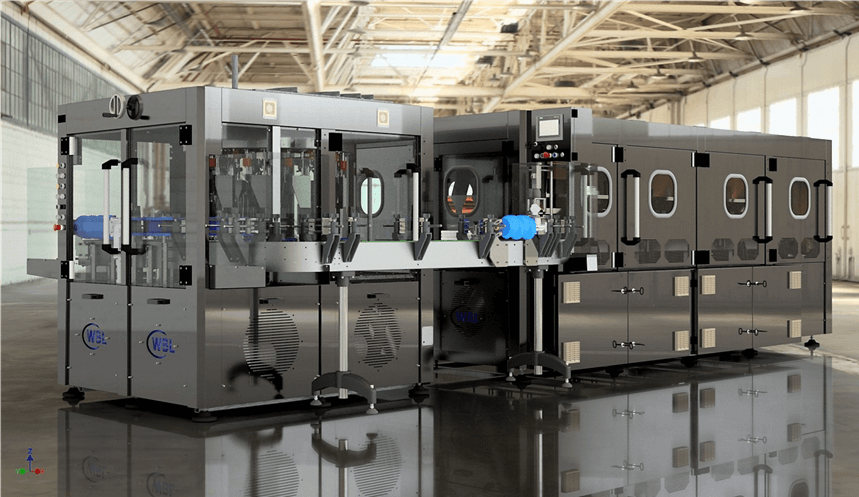
1 – “no water” device
2 – significantly reduced dimensions
3 – advanced catalytic technology System with an efficiency of 98,5 % as all energy is transformed without dispersion. No more plant engineering charged to the customer.
4 – Stationary treatment First machine in the world with stationary product treatment.
5 – “FIFO” device FIFO (“first in first out”) FIFO managed machine which guarantees traceability by batch and the staying time during the process. Uniformity of treatment.
6 – “Contactless” filling Bottles feeding method takes place without contact between the bottles. Relative noise is eliminated as well as the format change. For more information and to discover the range of products visit the site.